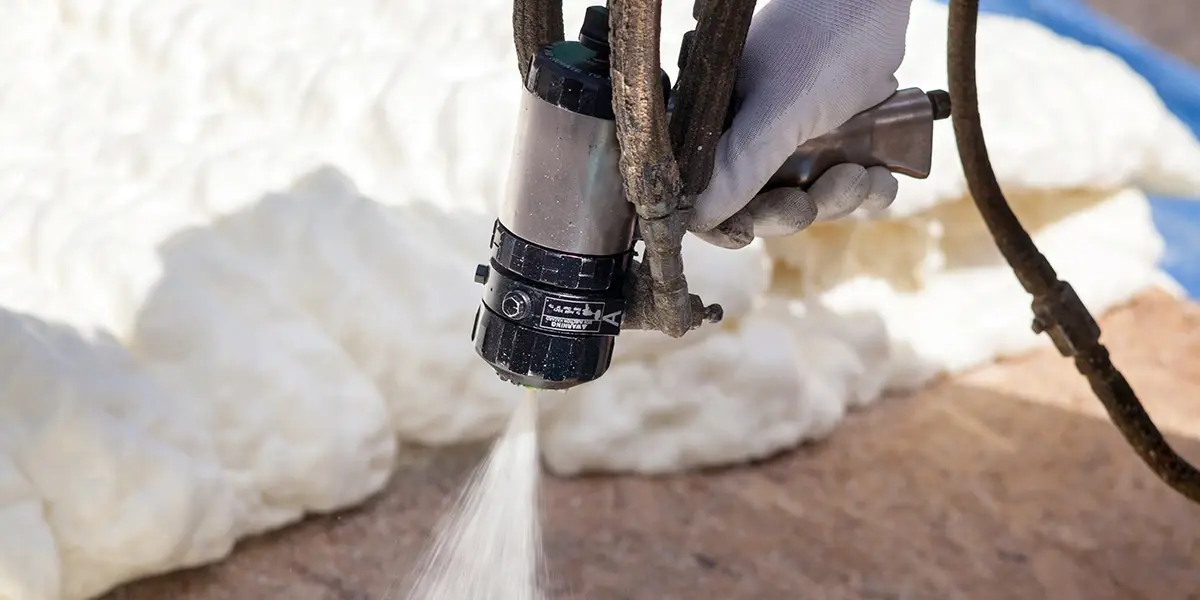
In industries that rely on chemical drum pumps, air motors, and mixers, ensuring optimal performance and equipment longevity is crucial. One of the best practices recommended for achieving this is proper lubrication. By implementing a lubrication system, companies can enhance the efficiency and lifespan of their equipment, ultimately leading to cost savings and improved productivity.
In this article:
- The Purpose of a Drum Pump
- How a Drum Pump Works
- Why Drum Pumps Need a Lubricator
- How Air Lubricators Work
- [VIDEO]: Best Practices for Air Motors and Drum Pumps
- Common Problems With Drum Pumps
- The Tsunami Solution: Air Lubricator Kit
WhAT IS the purpose of a drum pump?
A chemical drum pump is a highly specialized piece of equipment that facilitates the smooth transfer of liquids, particularly chemicals, from a large container or drum to a specific application. These pumps find extensive use in industrial environments and job sites, such as those involving spray foam applications.
How a drum pump works:
There are two main types of chemical drum pumps utilized in spray foam applications: diaphragm pumps and gear pumps.
-
Diaphragm Pump: Diaphragm pumps are highly sought after due to their ability to handle a wide range of viscosities, including thicker substances like foam. These pumps utilize a flexible diaphragm that moves back and forth, creating a seamless suction and discharge process. They are particularly well-suited for handling abrasive, corrosive, and viscous fluids without experiencing significant wear and tear.
-
Gear Pumps: Gear pumps are known for their accuracy and precise flow rates, making them ideal for applications that require precise dosing and uniform coverage. They operate by utilizing rotating gears to create a smooth and consistent flow of fluid. While gear pumps are effective for spray foam formulations with lower viscosities, they may not be as resilient when handling abrasive or corrosive materials compared to diaphragm pumps.
Regardless of the type of drum pump used, it is crucial to incorporate an air lubricator into the system.
why drum pumps need an air lubricator:
Lubrication plays a vital role in the smooth transfer of liquids, especially chemicals, from large containers or drums to specific applications. Chemical drum pumps are specialized equipment designed to facilitate this process. They are commonly used in industrial environments and job sites, such as those involving spray foam applications.
Drum pumps and agitators have moving parts that utilize compressed air to pull the chemical from the drum and push it downstream. These moving parts require a small amount of lubrication to prevent wear and tear on the system. Installing a lubrication kit at the point-of-use ensures that the equipment works better and lasts longer. The lubricator provides the necessary lubrication where it's needed, preventing premature equipment failure and optimizing performance.
Benefits of installing an air lubricator:
- Avoiding premature equipment failure from lack of lubrication
- Lubricating where it's needed, none where it's not
- Lubricating your pumps and mixer with one easy-to-install kit
- Regulator preventing over-pressurization and includes quick-connect fittings
How air lubricators work
Air lubricators function by atomizing small amounts of oil as air passes through the device. The atomized oil then lubricates the moving parts of the drum pump or agitator, ensuring smooth operation and reducing the risk of clogs.
To be effective, the lubricator should be installed close to the motor it is intended to lubricate. Placing the lubricator a few feet away from the motor is not as effective.
Common problem with drum pumps
One common problem with drum pumps is the freezing or frosting over of the pump due to rapid cooling caused by the escaping air. This phenomenon occurs as compressed air expands, and the air cools. However, using a regenerative dryer can help overcome this issue by operating at a much lower dew point compared to a refrigerated dryer.
Another problem that can arise is running straight line pressure into the air motor without lubrication. The piston running up and down in the air motor requires lubrication to function properly. To prevent piston failure, a lubricator may be installed in a system far away from the motor. However, this setup is not ideal and may not provide adequate lubrication.
The Tsunami Solution: Air Lubricator Kit
To address these challenges, the Tsunami Lubricator Kit offers an optimal solution. This kit includes two units, each equipped with a regulator to regulate air pressure, a lubricator, and quick connect fittings.
The first unit is designed to provide lubrication to the mixing pump while it is connected to the piston pump, ensuring proper lubrication at the point of use. It includes:
- Regulator to regulate air pressure
- Lubricator
- Whip hose to lubricate mixing pump while connected to piston pump
- Quick connect
The second unit is dedicated to lubricating the other pumps in the system, ensuring comprehensive lubrication coverage. It includes:
- Regulator to regulate air pressure
- Lubricator
- Quick connect
Questions? Ask the experts.
The proper air pressure into the pump can save wear and tear on the compressor. Using the correct regulator is crucial to ensure optimal pressure. Clean, dry air as well as proper lubrication and air regulation at the correct point are key to a successful job. Reach out to the team today with any questions.