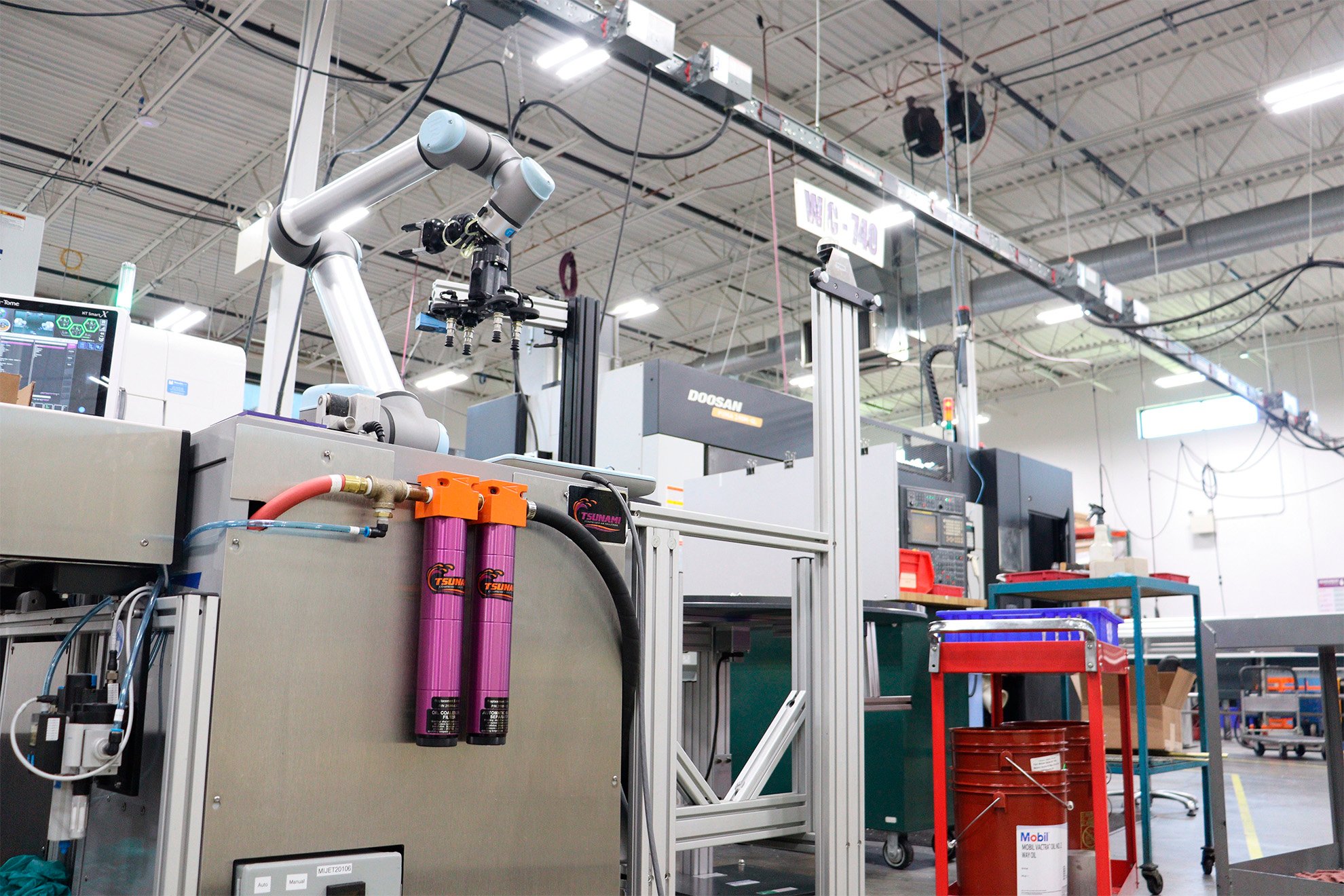
Enhancing Shop Efficiency: Industrial Air Dryers and Filters for Point of Use Air Treatment
Compressed air systems are essential to a wide range of operations in industrial settings, from powering tools to providing clean air for processes. But for many businesses, the efficiency of their compressed air system is an issue. Industrial air dryers are one way to optimize efficiency and get more out of your shop or factory's compressed air supply.
We'll explore different point-of-use (POU) applications where industrial air dryers provide tangible benefits in terms of cost savings and improved workflow. We'll look at the options available, along with best practices for getting the most out of your POU system.
jump to your application:
Select from the menu below to "skip" to the section.
importance of dry air for manufacturing
Known as the “fourth utility”, dry compressed air is a critical component in any manufacturing facility. The vast array of air-powered torque-drivers, pneumatic grippers, air presses, and impact wrenches demand consistently dry air for optimum reliability and service life.
Treating the compressed air in your shop shouldn’t be overlooked, air dryers and filters prevent condensation from degrading the performance of air devices located downstream. Failure to provide clean, dry air to such applications can cause expensive damages to equipment and even cause factory shutdowns.
Common issues that interfere with compressed air include:
-
Moisture: Humidity found in the ambient air is pulled into the compressor and condenses within the air lines.
-
Oil Contamination: Compressed air can contain oil particles; found in the ambient air or carried over from the compressor.
-
Particulate Matter: Small particles and debris can cause blockages in pneumatic systems.
-
Residual Contaminants: Desiccant dust or carbon can be released from low-quality, inadequate dryers and filters.
-
Incompatible Materials: Incompatible seals and gaskets can degrade in the presence of certain gases or liquids, resulting in contamination.
The contaminants listed above can cause the following:
- Corrosion, rust and damage to machines and components due to eroded lubrication
- Inconsistencies in spray-painting and powder coating
- Rusting & clogging of pneumatic tools
- Ice formation in cold, winter months
- Shortened-life of tools that run on gas and air
- Domino effects on all processes can lead to factory shutdowns and financial losses
How is dry air achieved in an manufacturing facility?
Hot, humid air exiting the air compressor needs to be treated before reaching a pneumatic application. To do so, manufactures should consider investing in an air dryer(s) to remove the humidity from the air stream. There are a few different air-drying methods: we recommend smaller point-of-use air dryers mounted as close to the application as possible.
Point-of-use air drying
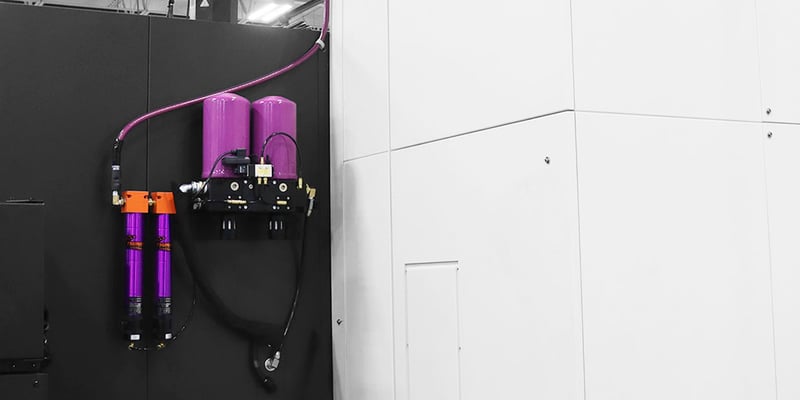
We refer to Point-of-Use Air Drying as the method of providing smaller, better dryers mounted in-line as close to the application as possible. This provides machines and processes the right air quality to achieve maximum performance in the most efficient way possible. Not every process requires the same quality of air. By treating air at the point-of-use, factories will see an increase in performance and efficiently in their processes.
Central air drying vs point-of-use air drying
Central air drying (the method of investing in a large air dryer, plumbed right next to the air compressor) may be effective for removing immediate liquids and particulates. What shops may not understand, is the liquids and particulates that can form inside the airlines downstream.
Remember that for every 20°F air cools, it will drop 50% of it’s moisture. This means that warm air immediately exiting the air compressor (and central air dryer) will still contain humidity.
Along with humidity not captured by the initial air dryer, there could be corrosion and particulates found in the air pipes that will be picked up from the air stream as well. All of these contaminates need to be removed before entering a machine or process.
Although central air dryers could be large and effective enough to remove contaminates at the compressor, the cost of operating such a large dryer for the entire shop will burn a hole in a factories pocket.
Investing in point-of-use air dryers will save manufactures costs in terms of efficiency and process performance. Let’s take a look at a few processes that may require additional treated air.
manufacturing applications requiring point-of-use air treatment
Plasma Cutting
Point-of-use compressed air filters improve the consistency of plasma cutting, allowing for sharper cuts, better accuracy, and extended tip life.
With point-of-use filters, there’s no need to worry about excess moisture or particles entering the machine. The last thing you want to do is prematurely replace an ultra-expensive plasma cutter or increase your consumable expenses. Point-of-use filters, along with regular air compressor maintenance, can help extend the machine's life.
Laser Cutting
We think of lasers as indestructible forces, but in manufacturing operations, they can be surprisingly finicky to keep in tip-top performance shape.
Compressed air point-of-use filters improve the efficiency of the laser cutting process by reducing:
- Debris
- Residue buildup
- Heat created by the machine
By using a point-of-use filter, businesses can reduce costs associated with maintenance or repair due to contaminants affecting cut quality.
Additionally, these filters also help maintain consistent production levels as they prevent any blockages caused by dirt or dust buildup over time.
CNC Machining
Finding the best air dryer for a CNC machine shop is important to ensure that the machining process runs smoothly. By carefully considering each type of dryer, it's possible to select one that absolutely meets your operation's specific needs. With the right dryer in place, you can be sure that your CNC machining projects will be successful and efficient.
Compressed air comes in handy for a number of situations, from keeping the workspace clear to actuating systems. For instance, the best air dryer for your shop will:
- Reduce contaminants -- A blast of dry air helps clear areas of debris, improves accuracy, and reduces tool damage. Otherwise, chips, dust, oil, dirt, and other contaminants interfere with the cutting tools and become embedded in the cutting surface.
- Improve actuating tool changes -- The compressed air flow controls the tool-changing process for rapid clamping, tightening, and release operations. This is managed by digital instructions already programmed into the system.
- Initializing robotic systems -- Air pressure powers robotic movements, which in turn assist with certain steps in the process, i.e. lifting, transporting, or placing products. Pneumatic systems replace both servo and electric motors.
Paintings & Coatings
While high humidity is an issue that auto body shops deal with on a regular basis, it is not the only potential environmental factor that interferes with a quality paint job.
Dust, oils, and other airborne contaminants are also pulled into the air stream from the compressor. Choosing an air treatment solution that removes this debris is crucial to the success of an auto body shop.
Tsunami Compressed Air Systems offers two different systems of air dryers to help with these issues. Both the Pure Series and Ultra Series systems provide dry compressed air that is cleaned of contaminants.
PURE SERIES – BUILD FOR PERFORMANCE AND EASE OF USE
- Available as a wall-mounted or tank-mounted option
- Offers two-stage Tsunami pre-filtration process (water separator & oil coalescing filter)
- Dual tower with automatic drains
ULTRA SERIES – BIGGER AND MORE FLEXIBLE
- Offers a more efficient system with a Programmable Logic Controller
- Comes with Moisture Minder pneumatic drains
- Factory expandable – filters are oversized to allow for additional dryer towers to be added if a shop/facility expanded its air requirements
- Rail-mounted option available
Powder Coating
Maintaining efficiency for air compressors in machine shops for powder coating projects means not only choosing the correct air dryer but making sure it is installed properly. The dryer should be able to maintain air pressure at the required levels and allow the powder gun to provide an even coat of powder.
Too much powder delivery decreases charging efficiency, which then dilutes the ability of the applicator to completely charge the powder. The problem then becomes poor transfer efficiency and reduced material utilization.
Preventing any premature tool failure– such as with the gun, hose, filters, or fluidizing plates-- saves on maintenance and tool replacement. Other situations that may point to the need for a new compressed air dryer include:
- Uneven powder transport
- Moisture in powder
- Oil in feed
- Contamination in the surrounding air
- Powder remnants or dirt in the coating booth, cyclone, or filter
- Solvent pops
- Blisters
- Poor fluidization due to powder clumping
Sandblasting
Point-of-use compressed air filters are essential for sandblasting machines to eliminate costly downtime.
They minimize condensation, preventing moisture from “clumping” your media during sandblasting operations and extending machine life by reducing impurities and wear on internal parts.
Grade D Breathing Air
Meeting Grade D breathing air requirements isn’t a one-time undertaking to tick a few boxes on a checklist. Rather, experts need to make meeting compliance standards part of daily routine – from equipment inspection & repair to ongoing employee education.
WHAT IS GRADE D BREATHING AIR?
Grade D breathing air is compressed air piped through a respirator and intended for use as breathing air by contractors handling harmful materials. In order to be considered Grade D breathing air, the following must be true:
- The air must be free of any notable odor
- Condensed hydrocarbons can’t exceed 5 mg/m
- Carbon monoxide can’t exceed 20 parts per million (ppm)
- Carbon dioxide must be less than 1,000 ppm
- Oxygen must be 19.5 to 23.5% (by volume)
Grade D breathing air is often supplied from a compressor system located within the application area. This allows for a constant flow of air during the entire application process. The compressor must be installed and maintained in accordance with CGA G-7 standards, and filters must be changed regularly to ensure maximum efficiency and safety.
selecting the right air dryer
To select the correct air dryer for your machine or process, refer to the manufactures handbook that came with the equipment to confirm the air demand for the machine. Once discovered, contact a premium air dryer manufacturer to select the right air treatment set-up for your machine.
What does Tsunami recommend for point-of-use air drying?
We recommend our Pure Series line of air dryers for treating air at the point of use. Using our pre-filtration and regenerative desiccant technology, operators can expect perfect air quality to get the job done. View our Pure Series line of air dryers or contact one of our experts to guide you to the perfect solution.
Tsunami Dryers | Streamlining Application
Tsunami Dryers can streamline the application process for air dryers, ensuring that each workshop receives the right equipment for their unique needs. Air dryers are highly effective in CNC machining, sandblasting, powder coating, and painting applications due to their ability to reduce moisture levels quickly and efficiently. With a wide selection of air dryers from Tsunami’s portfolio, customers have the flexibility to choose the perfect solution for their business.