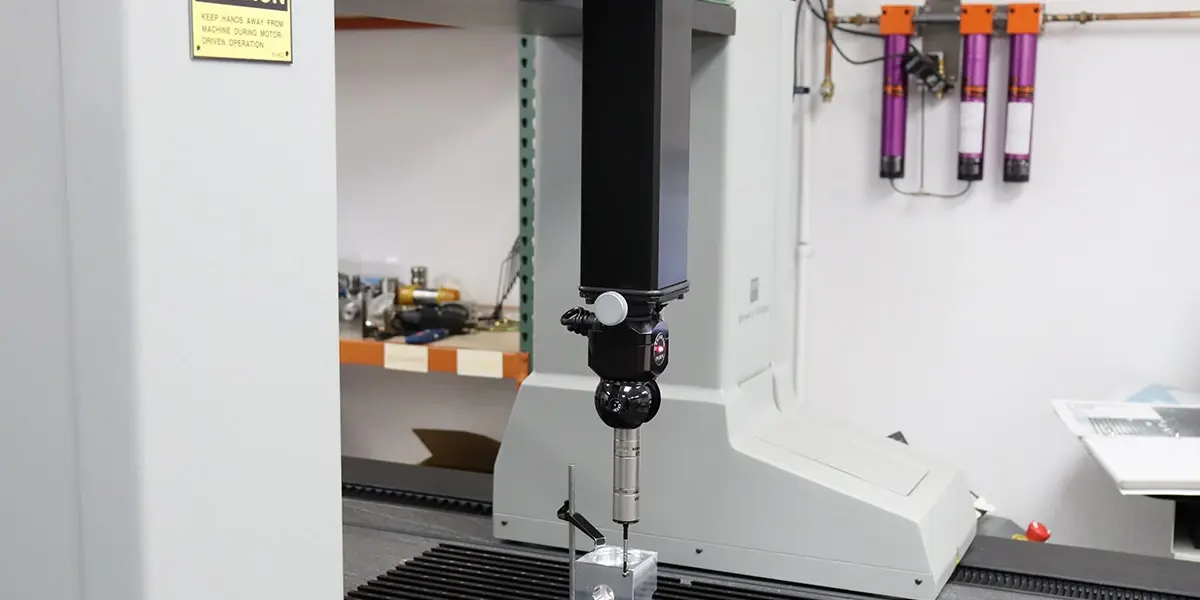
Industrial facilities require not just compressed air but the assurance of quality air being provided throughout their system. Putting a focus on point-of-use compressed air quality is essential for industrial facilities, ensuring they are providing the clean, dry air necessary for their products, tools, and machines. Optimizing your focus on point-of-use compressed air filters ensures that the cleanest, high-quality air is being provided to your equipment and applications.
In this article, we discuss:
- Benefits of Point-of-Use Focus for Compressed Air
- 5 Applications for Point-of-Use Compressed Air Filters in Industrial Facilities
- Plasma cutting
- Paintings and coatings
- CNC Machining
- Sandblasting
- Laser Cutting
- How Ineffective Filtration Impacts a System
Benefits of Point-of-Use Focus for Compressed Air
The main factors for improving compressed air quality that involve point-of-use filters:
-
Increase shop efficiency: Air isn't free! Using a large, centralized air dryer can be costly if the entire shop doesn't require the same clean air requirements. Prevent expensive air and electricity costs with point-of-use filters and dryers.
-
Extended life for the machine/tools: Reduce the amount of condensation and contaminants entering a machine or tool, extending its life and protecting your investment.
- Improved final product: Remove contaminants such as particulate, water, oil, and other impurities from the compressed air, resulting in air quality that can ultimately improve the final finished product.
While investing in point-of-use compressed air filters represents another up-front cost, industrial facilities will realize the long-term savings of reliable and improved system performance.
5 Applications for Point-of-Use Compressed Air Filters in Industrial Facilities
Industrial applications typically recommend/require a filter to be installed at the point of use to remove contaminants and cut down on debris that will interfere with your equipment’s ability to safely and effectively do its job. Here are five industrial applications where effective point-of-use compressed air filters can make a difference:
1. Plasma Cutting
Point-of-use compressed air filters improve the consistency of plasma cutting, allowing for sharper cuts, better accuracy, and extended tip life.
With point-of-use filters, there’s no need to worry about excess moisture or particles entering the machine. The last thing you want to do is prematurely replace an ultra-expensive plasma cutter or increase your consumable expenses. Point-of-use filters along with regular air compressor maintenance can help extend the machine's life.
2. Painting and Coatings
Filters in industrial painting and coating applications minimize contamination by removing particulates and other impurities from the air stream, helping to produce a higher-quality finish. Consistency in coating applications not only improves the finish but can help in reducing the amount of material used. As a bonus, you should see a reduction in additional labor costs when contaminated air requires a project to be reworked or resprayed.
A prime example of clean air in action is the reduction of “fisheyes” in auto paint.
Powder coating’s rep is that of higher-quality finishes than standard paint. As such, it requires a point-of-use filter to remove microscopic particles, moisture, and other contaminants that degrade surface smoothness and protection.
Air filters installed at the appropriate juncture ensure only clean and dry air will reach your powder coating equipment and guarantee a perfect finish every time. Additionally, these filtration systems help increase the efficiency of your system by preventing clogged or damaged parts caused by dirty air.
3. CNC Machining
The whole point of CNC workstations is to achieve reliable, precise results humans can’t achieve manually. It’s only logical you’d want to safeguard that advantage by setting up the machine for success.
For CNC machining applications, point-of-use air filters reduce contaminants in the system, and keep your internal air lines clear of water and debris which helps cut down on corrosion of system components. This leads to the machine producing a more accurate finished product and prevents premature aging of your equipment.
4. Sandblasting
Point-of-use compressed air filters are essential for sandblasting machines to eliminate costly downtime.
They minimize condensation, preventing moisture from “clumping” your media during sandblasting operations and extending machine life by reducing impurities and wear on internal parts.
5. Laser Cutting
We think of lasers as indestructible forces, but in manufacturing operations, they can be surprisingly finicky to keep in tip-top performance shape.
Compressed air point-of-use filters improve the efficiency of the laser-cutting process by reducing the:
-
Debris
-
Residue buildup
-
Heat created by the machine
By using a point-of-use filter, businesses can reduce costs associated with maintenance or repair due to contaminants affecting cut quality.
Additionally, these filters also help maintain consistent production levels as they prevent any blockages caused by dirt or dust buildup over time.
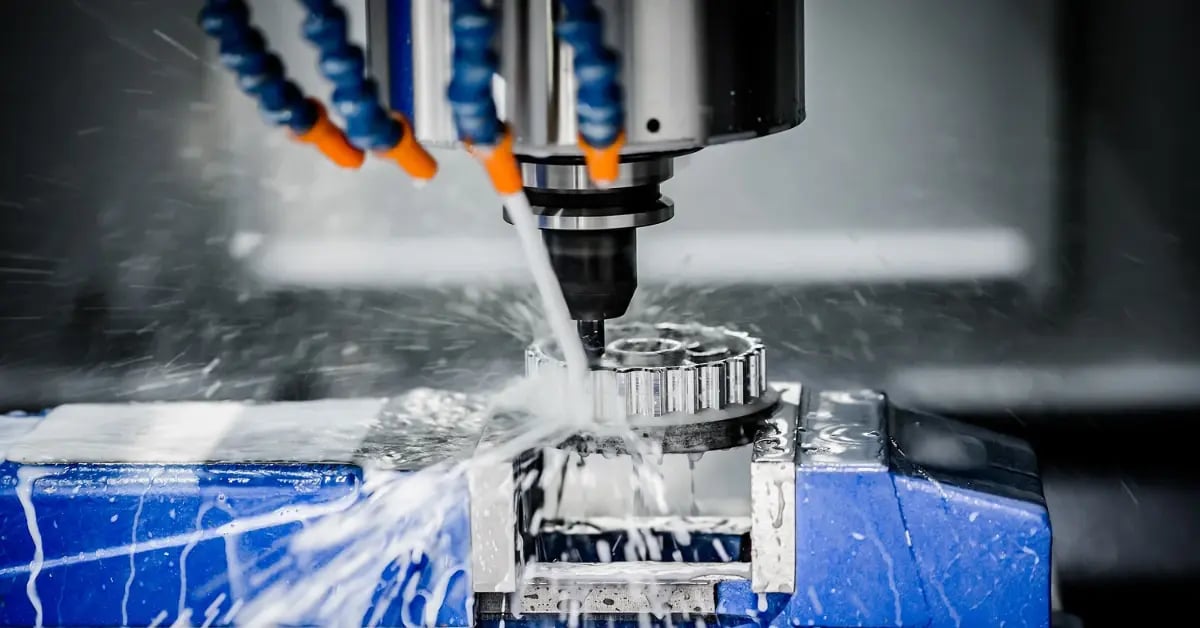
How Ineffective Filtration Impacts a System
From condensation and air tools corrupted by rust to downtime because the system isn’t running optimally, issues from a missing or misused filter mean money lost. While the loss of quality and efficiency is a common theme across the five cases above, each application has specific concerns you’ll need to address with your compressed air distributor.
Learn the Specific Needs of Your Compressed Air System
Concerned with the integrity of your operation’s air supply system? Ask an air filter expert about your shop's air dryer systems and the best layout for optimal efficiency.
Editor's Note: This blog post was originally published in 2022 and was updated in 2024 and 2025.