5 min read
Why You Need a Preventative Compressor Maintenance Plan
Tsunami Team
:
Jul 14, 2022 7:45:00 AM
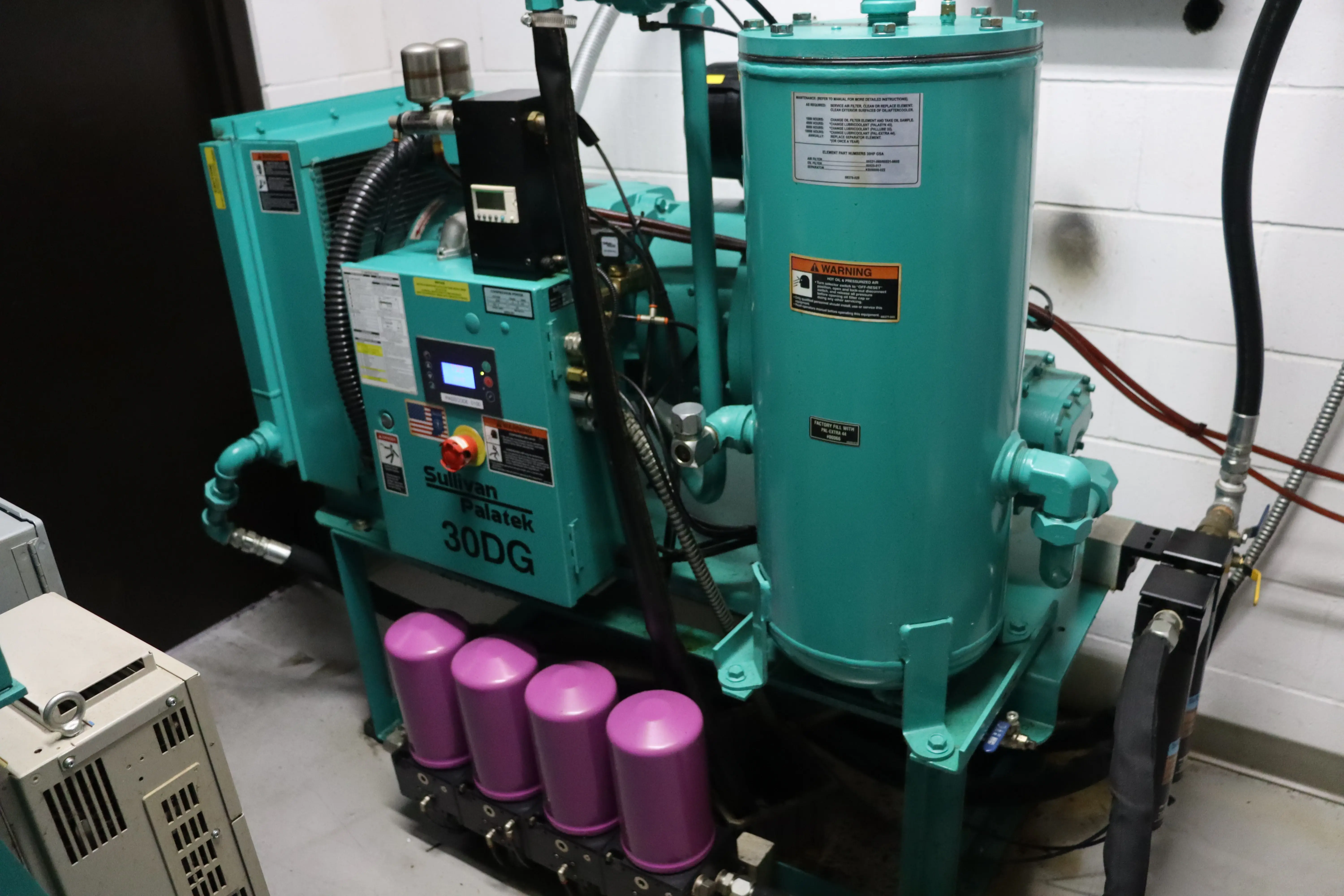
When it comes to the compressed air system in your workshop, the system’s efficiency is vital to overall performance and impacts system operational costs.
With any compressed air system, the goal is to operate it at the lowest pressure possible while maintaining sufficient energy for all operations and equipment. Operating at less than optimal pressure has a negative impact on tool performance and also on the quality of finished products.
According to the US Department of Energy, 20-30% of the average air compressor’s output is lost through air leaks. This means choosing an air compressor that best fits your workshop’s needs can mean significant savings over the course of the year.
Scheduled preventative compressor maintenance not only allows you to address potential problems before they have an impact on your work but also avoid shutdowns or product damage.
Make Preventative Compressor Maintenance a Priority
Whether your compressor is air-cooled, lubricant-injected, or lubricant-free, there are several tasks that should be handled on a routine basis to optimize its lifespan and maintain high performance.
Among the most common – and damaging – issues impacting compressed air system efficiency include:
- Condensation – a buildup of condensation can lead to rust and corrosion, damaged circuits and pneumatic controls, as well as ice buildup, clogged lines, or damaged equipment. Moisture can also reach the final product and cause damage or a decrease in quality (ex. the paint job on a vehicle).
- Contaminants – there are three types of contaminants that can end up in your compressed air system: water, solid particles, and oil. These contaminants can interfere with the efficiency of your compressed air system and its air purity. Contaminants clog valves, cylinders, and drains. Finally, contaminants can ruin a final product or reduce its quality – both bad for business.
[Checklist] Preventative Compressor Maintenance Schedule
Scheduled and comprehensive evaluations of your system help you save money, reduce system downtime, lower energy costs, and improve your compressor’s performance and efficiency. Always refer to the maintenance guide for your compressor for specific maintenance requirements.
As a guideline, a thorough preventative compressor maintenance schedule could include:
Daily
- Check lubricant levels, empty, and refill as necessary
- Check lubricant to make sure it is not discolored -- if discolored, it needs to be replaced
- Empty water out of the receiver tank
- Visually inspect compressor and check for leaks
- Monitor gauges for normal operation
- Observe for unusual noise/vibration
Weekly
- Check pressure relief valves
- Clean surfaces
- Inspect for air leaks
- Clean the air intake filter
Monthly
- Inspect the belt tension inside an air-cooled, reciprocating compressor
- Service the air filter
- Clean the aftercooler and fluid cooler fins
For a lubricant-injected rotary compressor:
- Wipe down the entire unit
Quarterly
For a lubricant-free, rotary screw compressor:
- Check the pressure drop over the filters
- Inspect filters for cleanliness and damage & replace as necessary
- Check the cooler
Biannually
For a lubricant-injected compressor:
- Take fluid samples and change the fluid filter
- Check the pressure relief valve
For a lubricant-free compressor:
- Clean the compressor
- Test the safety valve
- Inspect and clean the electronic drain
For an air-cooled compressor:
- Change out the lubricant
- Check valves for signs of leaks
- Clean the crankcase (don’t forget the strainer screen)
- Examine motor-area contact points
Evaluating Compressors Before Purchase
As compressors often represent a significant investment, it’s critical to take a hard look at the options available. One of the best resources to consult is a compressor’s manufacturer – they’re able to provide detailed information on performance, such as expected pressure drops.
Other elements to consider when assessing compressors include:
- Compressor requirements (and how they impact compressor performance)
- Ventilation requirements
- Storage tanks & drain types
Compressor Requirements
Plant volume requirements are the #1 factor for determining the size of the compressor needed. To determine compressor requirements for a new facility, it’s important to know the technical specifications for the equipment. Create a spreadsheet that includes data on:
- The minimum and maximum CFM required
- The minimum PSI requirements
- The amount of run time each shift for each piece of equipment
- The number of machines running at the same time
- The amount of time those machines will run simultaneously
- The various purposes of those machines
A compressor should typically be sized 10% larger in CFM output than the calculated total air volume requirement of a compressed air system. With these considerations accounted for, systems engineers are able to create estimates, which are usually higher than the actual CFM requirements for the facility. This is especially true when a mix of automatic and manual equipment is on the workshop floor.
Ventilation Requirements
Proper ventilation is important when syncing compressor requirements and the efficiency of the compressed air system setup.
Temperatures in air-cooled compressors are regulated by an internal fan pushing or pulling air across a radiator-style cooler. To maintain optimal cooling levels, the compressor must be located in an area that facilitates airflow. Remember: any ductwork connected to the machine must be sized correctly to keep the pressure drop under the maximum allowable threshold. If the ductwork is undersized, a booster fan may be necessary.
For a compressor located in an open room, the space must be large enough to dissipate the heat removed from the compressor (a 100 HP compressor will exhaust 250,000 BTU/hr into a room). If the room is not large enough, an exhaust fan larger than the compressor fan should be installed.
Storage Tanks & Drain Types
Condensation can seriously interfere with system efficiency. Therefore, appropriately sized storage tanks and ensuring the correct drains are installed are key components to keep your system operating at top efficiency. The rule of thumb is three gallons of stored air for every CFM the compressor generates. Compressor size, reliability of your memory, and atmospheric conditions are all important considerations for the type of drain to install.
There are a number of different types of drains often used:
- Internal float drains
- External float drains
- Pneumatically controlled drains
- Electronic drain valves
Internal Float Drains
This type of drain has two versions:
- A normally open internal float drain requires air pressure to seal the discharge orifice.
- A normally closed internal float drain only opens the discharge port to purge collected moisture when the level of the condensate lifts the float to a set level.
External Float Drains
This drain type operates in a manner similar to the normally closed internal float drain. However, they are contained in their own remote housing.
Pneumatically Controlled Drains
Pneumatically controlled drains come in two types:
- A pneumatic level sensing drain uses a mechanical float within a reservoir, which controls a pneumatic cylinder. That cylinder is connected to a ball valve, and it avoids the loss of compressed air when it actuates.
- A pneumatic piloted drain receives a signal, typically from the compressor’s unloading circuit. The signal allows moisture to collect in a temporary reservoir and allows the condensate to be discharged when the signal is removed.
Electronic Drain Valves
Electronic drain valves consist of an adjustable electric timer, which is attached to a solenoid valve. The timer actuates the solenoid valve, expelling condensate out the discharge port and typically releasing some compressed air as well.
A strainer should be installed ahead of the solenoid valve to reduce the risk of blockage from particulates.
A Word on Manual Drains
A final option is a manual drain, which requires periodic draining by an operator. These are usually simple valves. The best use case for these valves are areas where condensate is low or nonexistent.
Preventative Compressor Maintenance = Operational Efficiency
Time is money for any business. Choosing to set aside time for preventative compressor maintenance is a valuable investment, helping your operation avoid the significant cost and loss of work due to a system shutdown.
Setting a preventative maintenance schedule based on your compressor's manufacturer's guide, similar to the one above, allows you to break the maintenance cycle into manageable parts and keep your system running the way it should.
Remember: Having the right compressor for your workshop and installing accessory parts to support the system efficiently will also help reduce future maintenance issues.
Consult the Experts
The Professionals at Tsunami Compressed Air Systems are well-versed in the different preventative maintenance schedules and can guide you through the process of choosing the right drain.