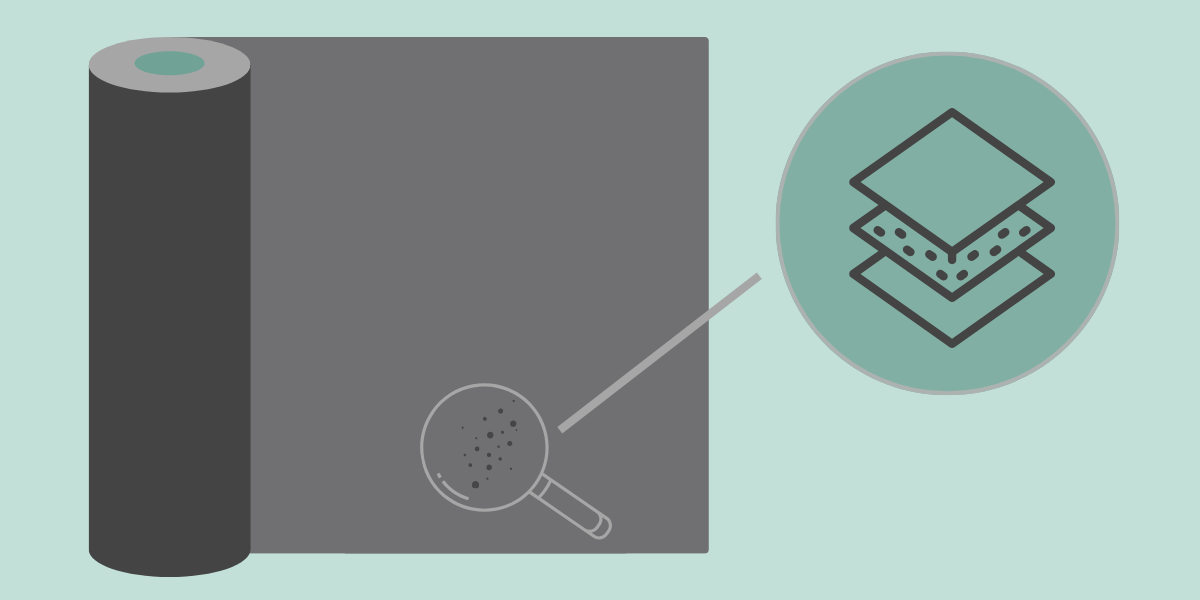
Equipment exposed to a variety of conditions - whether it'd be extreme heat, bitter cold, and everything in between, a barrier is required to ensure they remain at an optimal temperature to keep operations running smoothly. Failure to invest in such technology could result in unexpected downtime and expensive repairs.
In this article, we are discussing the benefits of a custom cover, and what the process looks like:
- The Utility of Custom Insulation Covers
- Designing Your Custom Cover
- Custom Textile Industry Manufacturing Solutions
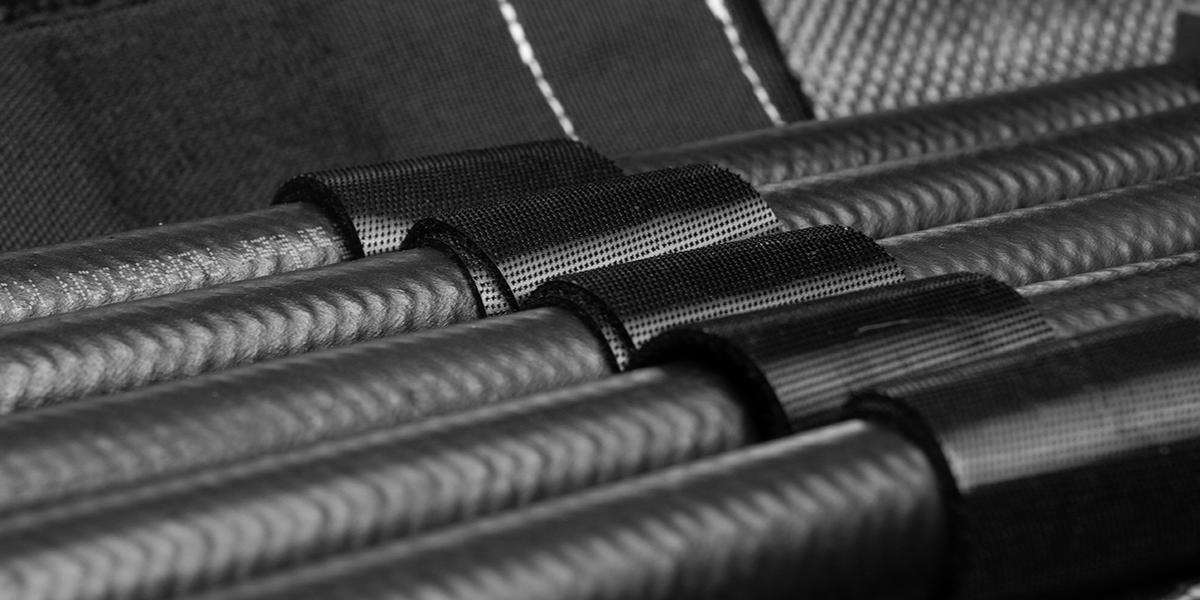
The Utility of Custom Insulation Covers
Insulation covers are important in protecting your hoses and equipment, no matter the ambient conditions of the environment they're in. Having an insulation cover you can depend on has many long-term benefits to your equipment and the efficiency of your business; especially when it's designed for your equipment alone.
Here are some of the main benefits of having an insulation cover made to perfectly fit your equipment:
- Longer lasting equipment: insulation covers protect your equipment to help prevent wear and tear while simultaneously keeping the contents an optimal temperature; this prevents punctures and rips from the outside, and corrosion, boiling, or freeze up on the inside. An insulation cover has the potential to protect your equipment from the inside-out.
- No hold ups: due to the insulating properties, having a cover made to fit your application ensures everything is working optimally; this means goodbye to clogged hoses or melting contents that can hold a process up or be detrimental to the task at hand.
- Less maintenance: a made-to-fit cover maintains optimal performance which will result in less maintenance and fixes beyond what the equipment already requires. No more pauses to unclog or cool down equipment on the verge of overheating or vice versa.
- Decrease downtime: having a reliable insulating cover decreases the amount of downtime needed to fix problems or troubleshoot other issues.
- Increase your ROI: by investing in a custom insulated cover for your application, you can save time and money on repairs or replacements that used to plague your equipment and operations.
How to Design an Insulation Cover
Designing an insulation cover is a considerably straightforward process. Most textile manufacturers will work with you from ideation to creation to ensure every part of the cover meets the criteria necessary to serve your application needs.
There are 5 steps to the custom insulated cover process:
- Define the Problem and Desired Solution
- Select Materials for the Design
- Design the Cover
- Production
- Distribution
1. DEFINE THE PROBLEM AND DESIRED SOLUTION
Along with gathering measurements and general movement of the application a cover will be designed for, there is additional information vital for creating the ideal insulated cover. It's important to consider what the cover generally needs to accomplish (ex. safety, temperature regulation, performance, etc.). It's also important to consider if the cover is meant for configurable parts or total custom parts.
Common questions asked when defining the problem for configurable parts:
- Is abrasion a factor?
- Is temperature a factor?
- What is the end use?
- Does the closure need extra enforcement?
- Does it need straps to secure the sleeve?
- Does it need to be fastened to anything on the ends?
When considering completely custom parts to solve a problem, there's a different set of questions to consider:
- What is the part that needs protecting?
- What is the max running temperature?
- What are you needing protection for? (Human touch? Protecting cables? Ambient conditions?)
- Will the part see inclement weather (outdoor abrasion from dirt, sand or any other abrasive elements)?
These is a non-exhaustive list of questions you should keep in mind, or may be asked when going through the process. Understanding the desired outcome and temperature requirements will be pertinent in contracting your part out to a textile provider.
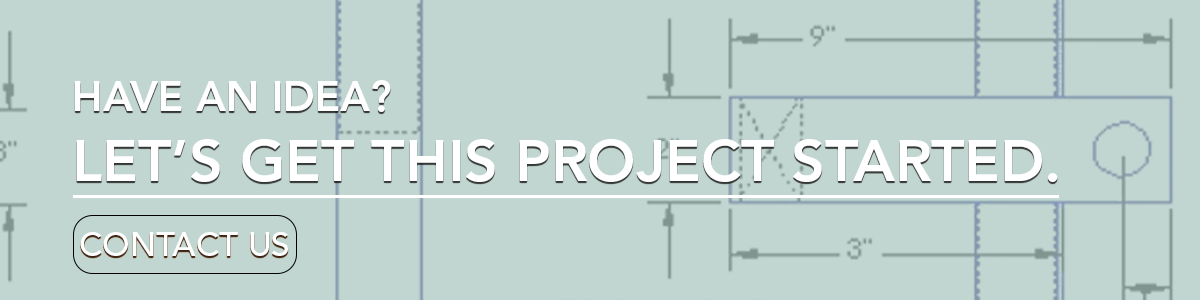
2. Select materials for design
In the world of custom textiles, there are a variety of options. As for insulated covers meant to last and get you the results you are looking for: there is a fabric made for your specific needs and requirements. This all depends on the environment the equipment is in and the results you are aiming to achieve with the equipment.
When looking at fabric options, it can be overwhelming because of the variety of properties each one possesses. We are going to break down the most common fabrics and their characteristics for better understanding of what you may need for your insulated cover solution. A textile expert will ultimately choose the fabric that will benefit the application your custom insulation cover is designed for.
The main questions asked for material selection are: What materials will work with the part that needs protection? How many layers of protection do we need to accomplish the need of the customer? What closures will work? What threads will work?
Most Common Fabrics
-
-
Iridium liners: made of an industrial liner with the ability to lower temperatures up to 200°F.
-
PAN felt fibers: a flame-resistant material made to withstand temperatures up to 1800°F. Two layers of silica-like felt are placed in the middle of a cover.
-
Insilflex: flame and chemical resistant and rated for temperatures up to 600°F, it's used as the outermost layer of a cover because heat dissipates in the material.
-
Temp mat: a compressed fiberglass material that is heat resistant, flexible, and offers low thermal conductivity.
-
Ceramic paper: can withstand temperatures up to 2400°F, this material is considered a super-insulator due to its light weight, rigidity, and ability to hold insulation.
-
Silitex: made of silica, this material is intended for protection in high temperatures and is usually placed on the inner lining of a custom cover.
-
Radiant liner: reflects heat and cool air in an effort to maintain optimal temperature.
-
3. Design the Cover
Now that you've defined the problem and understand the material requirements, it's time to design the cover! At this stage in the process, a textile solutions provider will create a prototype for your application.
Important questions to have answers to:
- Does the cover need to be removable?
- If removable, what kind of fasteners would you prefer?
- Is there enough area surrounding the application for the desired cover thickness?
- What is the targeted budget and the timeline for your project?
Once any remaining questions are answered, a prototype will be made. The insulation cover prototype will undergo testing to ensure it will work for the application its designed for, and any adjustments will be made if deemed necessary. When the design is perfected and the cover works as intended, the final steps are production and distribution.
4. Insulated Cover Production
When the prototype is approved, the production timeline is established. The timeline depends on the demand of the cover, the time it will take to manufacture the covers needed, and amount of specifications required to complete the covers. The production also includes the necessary quality testing needed before it is distributed. Once this has been decided, mass production begins.
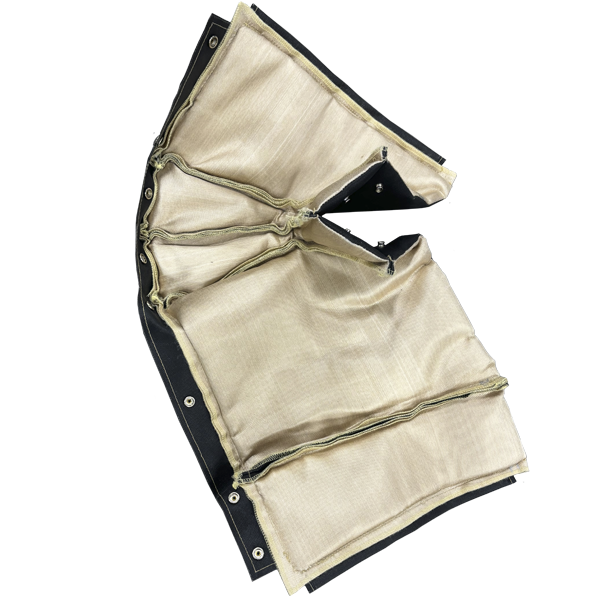
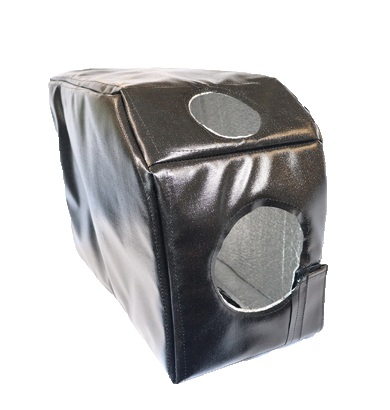
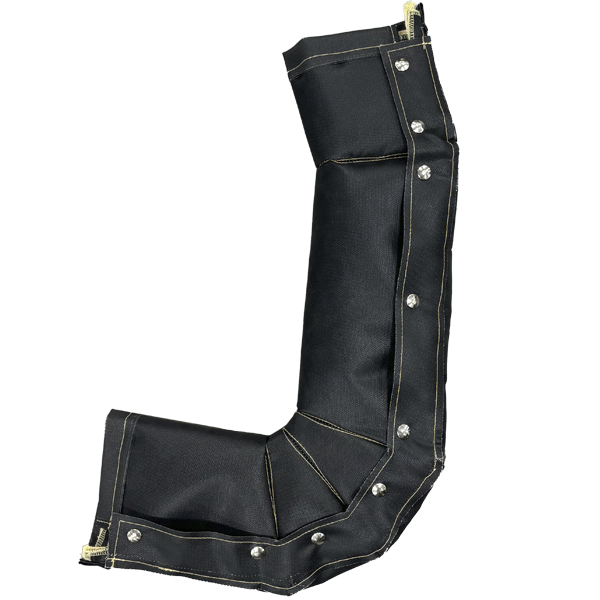
5. Distribution
Distributing the insulated covers is the final step of the cover process. Distribution is carried out by the custom textile shop or a third party; whichever is more efficient to get the covers where they need to be at the most profitable price point for you.
Custom textile Industry Manufacturing Solutions
Creating a custom insulation cover can be extremely beneficial to your equipment and applications by increasing their life, decreasing the amount of maintenance required, and protecting it from potentially dangerous conditions. Not only is a cover good for your equipment, it greatly benefits your business. Having a cover to perfectly fit your equipment increases the safety of the worksite, lowers costs, decreases downtime, and increases ROI over time.
By having a custom cover, you can save yourself from worrying about potentially having to spend exorbitant amounts of money to fix or replace equipment, or worrying an application will falter due to not having a cover to keep operations running as intended.
If you're ready to change the way your industry operates and invest in a protection solution, Python Protective Sleeves and Covers has everything you need. Say goodbye to overheated, frozen, or battered equipment - and say hello to a team that cares about you having successful, safe, and reliable operations all year long.