Guide to Custom Textile Manufacturing: From Fundamentals to Industry Applications
Custom textile manufacturing isn’t just about producing fabric - it’s about engineering a solution that meets a specific set of needs. With challenges ranging from environmental durability to specialized performance criteria, custom textiles have revolutionized the industrial manufacturing, agriculture, and government sectors. By integrating innovative design with advanced production methods, manufacturers can deliver solutions tailored for enhanced protection, performance, and longevity.
Whether you’re looking to learn the basics of custom textile manufacturing or need tips on finding the right partner, this guide will walk you through everything you need to consider. We’ve gathered key insights on design, manufacturing quality, and practical application to help you make informed decisions.
What is Custom Textile Manufacturing?
Custom textile manufacturing involves designing, fabricating, and converting materials to meet specific requirements in durability, functionality, and aesthetic appeal. This process often includes collaboration with engineering teams to transform original fabrics into specialized products through methods like rotary die cutting and assembly.
What can you manufacture with textiles?
The sky’s the limit when manufacturing textiles - especially for industrial purposes. When working on a job site or in a factory, there are many aspects to consider for improvement. Maybe wires and cords need to be held together, but there isn’t a band large and strong enough to keep them together, or they get tangled too often, resulting in restarting machines. When nothing on the market has what you need, custom textile manufacturing comes in.
Instead of making an exhaustive list of what textile manufacturers can do, here are a few examples:
-
Bundling Straps
-
Custom Straps
-
Heated Cover
-
High-Temperature Covers
-
Energy Chain Covers
-
Custom Grommets
-
Insulated Covers
-
Protective Sleeves
-
Electric Sleeving
-
Protective Gear
-
Bundling Straps
-
Custom Straps
-
Heated Cover
-
High-Temperature Covers
-
Energy Chain Covers
-
Custom Grommets
-
Insulated Covers
-
Protective Sleeves
-
Electric Sleeving
-
Protective Gear
And that’s just the beginning. If you have an idea, a design team of engineers will make it come to life. Or if you have a problem and still need a solution, a manufacturer can come up with the idea, too.
We'll expand more in-depth on the custom applications below, or you can click here to jump to that section.
The Custom Textile Manufacturing Process: From Design to Distribution
No matter the project, custom textile manufacturing involves multiple stages to transform raw materials into specialized products. Here's a closer look at the key steps involved:
1. Design & Engineering
During this stage, the manufacturer collaborates with you to understand the intended application and functional requirements of your textile product. Material selection is a key focus, ensuring a balance of durability, flexibility, and environmental resistance. Prototyping and early-stage testing help minimize production errors and validate performance before full-scale manufacturing begins. Using CAD (computer-aided design) software, manufacturers can visualize the final product, making precise adjustments to reinforcements, seam placements, and overall construction for optimal functionality.
2. Material Selection & Sourcing
Once the design is finalized, the next step is material selection and sourcing. Manufacturers choose from synthetic, natural, or blended fabrics, considering factors like strength, water resistance, and UV protection. Specialized coatings, laminates, or reinforcements may be incorporated to enhance the fabric’s performance, ensuring compliance with industry standards such as heat resistance for industrial applications or antimicrobial properties for healthcare textiles.
3. Cutting & Fabrication
With materials secured, the cutting and fabrication phase begins. Techniques such as hot air welding and wedge welding capabilities, or CNC cutting are used to shape textile components with precision. Assembly methods vary depending on the product’s requirements, ranging from traditional sewing to heat sealing for waterproof and airtight seams. Reinforcements, such as double stitching, binding, or additional fabric layers, are often applied to improve durability in high-stress areas.
4. Customization & Special Features
For products that require additional customization, manufacturers integrate special features such as branding elements, logos, or unique color patterns. Functional enhancements, including weatherproof coatings, antimicrobial treatments, or reflective materials, may also be applied. Fasteners like snaps, military-grade hook and loop, or straps are added when adjustable and secure fittings are needed.
5. Quality Control & Testing
Before a product is finalized, quality control and testing play a critical role in ensuring consistency and reliability. Stress tests assess tensile strength and wear resistance, while waterproofing, UV resistance, and temperature tolerance are verified for specialized applications. Manufacturers carefully inspect stitching, seams, and finishing details to maintain high-quality standards and eliminate defects before shipment.
6. Packaging
After inspection, products move to the packaging stage. Once assembled, each item goes through a final quality check before being securely packaged to protect it during transit.
7. Distribution & Delivery
The final step in the process is distribution and delivery. Manufacturers manage logistics to ensure products reach their destinations on time, often providing documentation, installation guides, or usage instructions as needed.
Working with a manufacturer that oversees all seven stages ensures a seamless design and production experience.
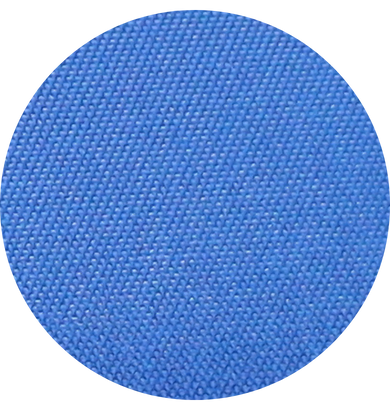
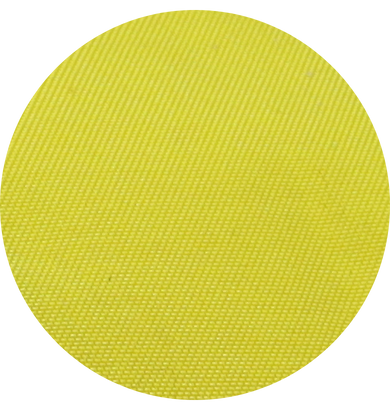
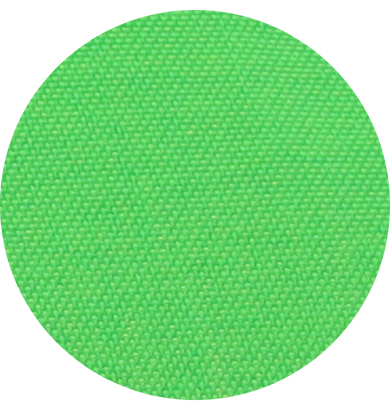
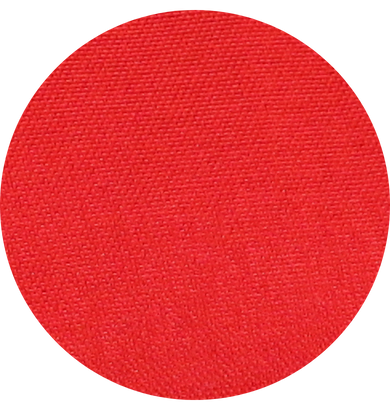
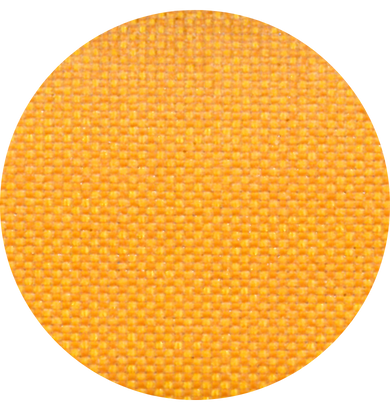
Signal Fabric
Signal fabric is a durable, high-visibility textile commonly used in applications where safety and visibility are priorities. It is often seen in industrial covers, protective gear, and outdoor applications where bright, reflective materials help enhance visibility in low-light conditions. This fabric is designed to withstand harsh environmental conditions while remaining lightweight and flexible.
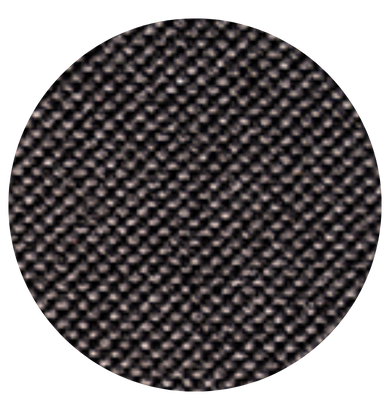
Black Poly (Black Polyester) Fabric
Black poly is a versatile, high-strength polyester fabric known for its durability and resistance to wear and tear. It is often used in industrial and outdoor applications due to its UV resistance, water repellency, and abrasion resistance. Common applications include protective covers, storage bags, and custom enclosures for equipment and machinery. Black poly is also a preferred choice for military and tactical gear due to its low visibility and robust performance in demanding environments.
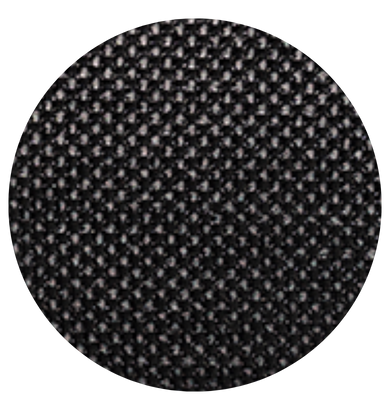
1050B (1050B Ballistic Nylon) Fabric
1050B refers to 1050 denier ballistic nylon, a highly durable and abrasion-resistant fabric designed for extreme conditions. Originally developed for military body armor, 1050B is now widely used in heavy-duty straps, tactical gear, and protective cases. Its tightly woven construction offers superior resistance to punctures and tears, making it ideal for high-impact environments where strength and toughness are required.
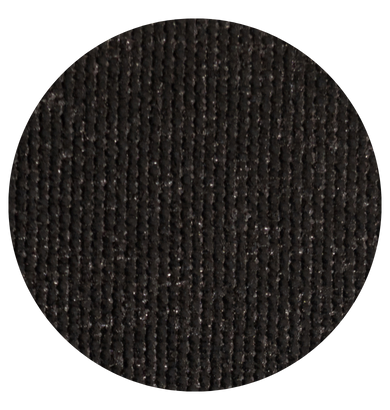
5601 Fabric
5601 fabric is a high-performance industrial textile used in applications where strength, weather resistance, and flexibility are key concerns. It is commonly utilizes in agricultural equipment covers, heavy-duty straps, and protective enclosures. Its construction makes it suitable for outdoor and industrial environments where exposure to UV rays, moisture, and abrasions is common.
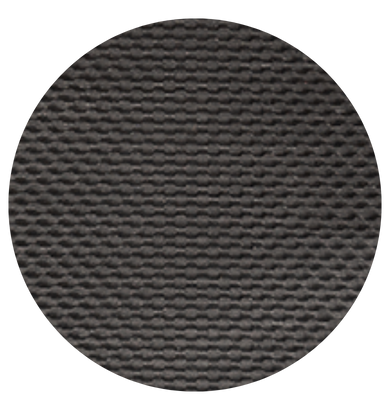
18411 Fabric
18411 is a specialized textile known for its durability and application versatility. it is frequently used in custom industrial covers, protective sleeves, and high-strength bag applications. This fabric is designed to provide enhanced resistance to harsh conditions while maintaining flexibility for ease of use in manufacturing and product design.
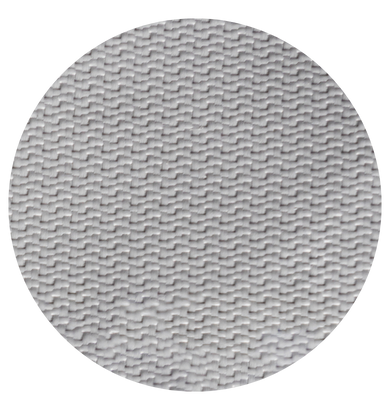
TGS Fabric
TGS fabric is a heavy-duty, reinforced textile designed for high-stress applications. It is often chosen for bundling straps, harness systems, and industrial-strength fastening solutions. Known for its high tensile strength and abrasion resistance, TGS fabric is particularly valuable in transportation, logistics, and manufacturing, where securing heavy loads is a priority.
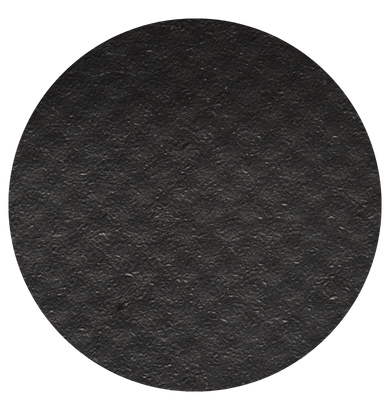
40HDA
40HDA fabric is a high-density textile designed fir specialized applications requiring rigidity, weather resistance, and long-term durability. It is commonly found in heavy-duty tarps, industrial curtains, and custom enclosures for machinery. This fabric provides excellent UV resistance and waterproof properties, making it suitable for outdoor and high-exposure environments.
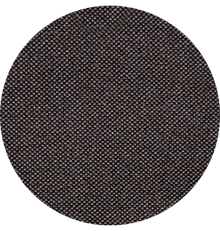
Black Poly (Black Polyester) Fabric
Black poly is a versatile, high-strength polyester fabric known for its durability and resistance to wear and tear. It is often used in industrial and outdoor applications due to its UV resistance, water repellency, and abrasion resistance. Common applications include protective covers, storage bags, and custom enclosures for equipment and machinery. Black poly is also a preferred choice for military and tactical gear due to its low visibility and robust performance in demanding environments.
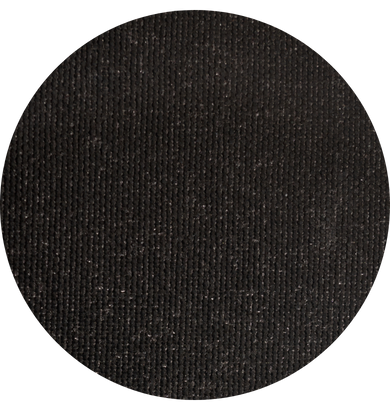
1050B (1050D Ballistic Nylon) Fabric
1050B refers to 1050 denier ballistic nylon, a highly durable and abrasion-resistant fabric designed for extreme conditions. Originally developed for military body armor, 1050B is now widely used in heavy-duty straps, tactical gear, and protective cases. Its tightly woven construction offers superior resistance to punctures and tears, making it ideal for high-impact environments where strength and toughness are required.
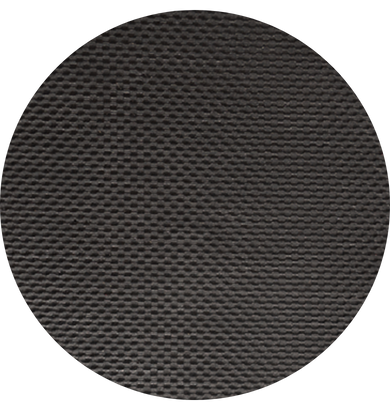
5601 Fabric
5601 fabric is a high-performance industrial textile used in applications where strength, weather resistance, and flexibility are key concerns. It is commonly utilizes in agricultural equipment covers, heavy-duty straps, and protective enclosures. Its construction makes it suitable for outdoor and industrial environments where exposure to UV rays, moisture, and abrasions is common.
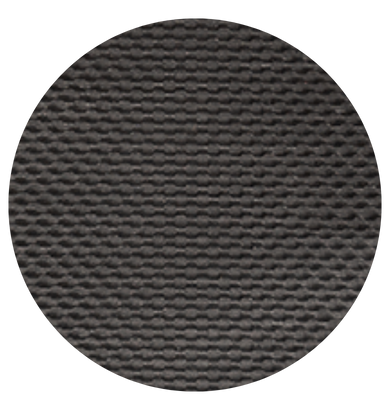
18411 Fabric
18411 is a specialized textile known for its durability and application versatility. it is frequently used in custom industrial covers, protective sleeves, and high-strength bag applications. This fabric is designed to provide enhanced resistance to harsh conditions while maintaining flexibility for ease of use in manufacturing and product design.
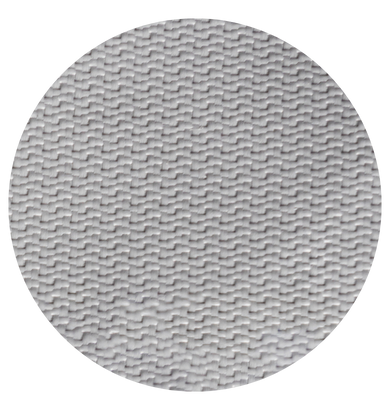
TGS Fabric
TGS fabric is a heavy-duty, reinforced textile designed for high-stress applications. It is often chosen for bundling straps, harness systems, and industrial-strength fastening solutions. Known for its high tensile strength and abrasion resistance, TGS fabric is particularly valuable in transportation, logistics, and manufacturing, where securing heavy loads is a priority.
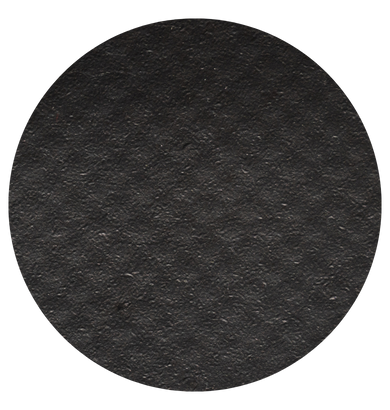
40HDA Fabric
40HDA fabric is a high-density textile designed fir specialized applications requiring rigidity, weather resistance, and long-term durability. It is commonly found in heavy-duty tarps, industrial curtains, and custom enclosures for machinery. This fabric provides excellent UV resistance and waterproof properties, making it suitable for outdoor and high-exposure environments.
Choosing the Right Fabric for Your Application
When selecting a fabric for a custom textile project, it’s essential to consider the specific requirements of your application, including:
Abrasion Resistance for industrial covers, straps, and tactical gear
UV & Weather Resistance for outdoor applications and protective covers
Textile Strength & Tear Resistance for securing outdoor applications and protective covers
Flexibility & Weight for applications that require movement and ease of handling
Water & Chemical Resistance for industrial, medical, and military uses
By working with a manufacturer experienced in custom textile solutions, you can ensure you’re selecting the best fabric for your needs, maximizing durability, efficiency, and performance in your final product.
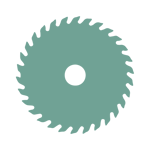
Abrasion Resistance
for industrial covers, straps, and tactical gear
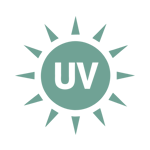
UV & Weather Resistance
for outdoor applications and protective covers
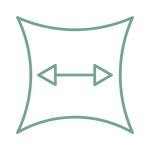
Textile Strength & Tear Resistance
for securing outdoor applications and protective covers
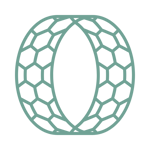
Flexibility & Weight
for applications that require movement and ease of handling
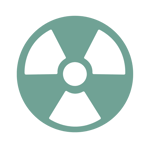
Water & Chemical Resistance
for industrial, medical, and military uses
By working with a manufacturer experienced in custom textile solutions, you can ensure you’re selecting the best fabric for your needs, maximizing durability, efficiency, and performance in your final product.
Common Applications of Custom Textiles
Custom textiles are essential across many industries, providing tailored solutions that enhance functionality, safety, and durability. Whether used for agricultural equipment, industrial machinery, or specialized protective gear, custom fabrics play a critical role in optimizing performance and extending the lifespan of products. Below are some of the most common applications of custom textiles:
Agriculture & Farming
In the agricultural industry, custom textiles can improve efficiency and protect equipment and operators. Heavy-duty fabrics are designed to withstand harsh outdoor conditions, including exposure to sunlight, moisture, and fluctuating temperatures. Examples include hay and forage netting, calibration bags for precision planting, and wheel-motor hose covers used in crop sprayers to prevent wear and tear. These textiles help reduce downtime, protect expensive machinery, and enhance overall productivity in farming operations.
Industrial Equipment & Manufacturing
Custom textiles play a significant role in industrial settings, where they are used for machine covers, protective sleeves, and bundling straps. Many of these textiles are engineered with high-strength materials that resist abrasion, chemicals, and extreme temperatures. Industrial covers, for example, shield sensitive machinery from dust, debris, and moisture, extending equipment lifespan and reducing maintenance costs. Insulated covers are commonly used in manufacturing environments to regulate temperatures and prevent energy loss, improving efficiency and worker safety.
Powersports & Recreational Vehicles
Powersports equipment, including ATVs, motorcycles, and personal watercraft, requires durable textile solutions to withstand rugged conditions. Custom textile applications in this sector include protective covers, weather-resistant storage bags, heavy-duty straps, and gear organizers. These products are often designed to be UV-resistant, water-repellent, and impact-resistant to ensure long-term durability. Protective covers help shield vehicles from environmental elements when not in use, while custom straps and fasteners enhance safety and security during transportation.
Military & Tactical Gear
Custom textiles are widely used in military and defense applications, where durability and functionality are paramount. Military-grade fabrics are engineered to resist extreme weather, abrasions, and impact forces. Examples include camouflage netting, tactical gear pouches, and protective covers for sensitive equipment. These textiles often feature reinforced stitching, water-resistant coatings, and fire-retardant properties to ensure reliability in harsh environments.
Outdoor & Recreational Gear
From camping gear to sporting equipment, custom textiles are vital in the outdoor industry. Weather-resistant fabrics are used for awnings, and protective coverings to shield against the elements
Fire & Safety Equipment
Fire-resistant textiles are essential in industries where workers are exposed to high temperatures, spark and spall, or hazardous chemicals. A custom textile manufacturer can cut and sew custom products like welding curtains and industrial safety covers using materials that meet strict safety standards.
Agriculture & Farming
In the agricultural industry, custom textiles can improve efficiency and protect equipment and operators. Heavy-duty fabrics are designed to withstand harsh outdoor conditions, including exposure to sunlight, moisture, and fluctuating temperatures. Examples include hay and forage netting, calibration bags for precision planting, and wheel-motor hose covers used in crop sprayers to prevent wear and tear. These textiles help reduce downtime, protect expensive machinery, and enhance overall productivity in farming operations.
Industrial Equipment & Manufacturing
Custom textiles play a significant role in industrial settings, where they are used for machine covers, protective sleeves, and bundling straps. Many of these textiles are engineered with high-strength materials that resist abrasion, chemicals, and extreme temperatures. Industrial covers, for example, shield sensitive machinery from dust, debris, and moisture, extending equipment lifespan and reducing maintenance costs. Insulated covers are commonly used in manufacturing environments to regulate temperatures and prevent energy loss, improving efficiency and worker safety.
Powersports & Recreational Vehicles
Powersports equipment, including ATVs, motorcycles, and personal watercraft, requires durable textile solutions to withstand rugged conditions. Custom textile applications in this sector include protective covers, weather-resistant storage bags, heavy-duty straps, and gear organizers. These products are often designed to be UV-resistant, water-repellent, and impact-resistant to ensure long-term durability. Protective covers help shield vehicles from environmental elements when not in use, while custom straps and fasteners enhance safety and security during transportation.
Military & Tactical Gear
Custom textiles are widely used in military and defense applications, where durability and functionality are paramount. Military-grade fabrics are engineered to resist extreme weather, abrasions, and impact forces. Examples include camouflage netting, tactical gear pouches, and protective covers for sensitive equipment. These textiles often feature reinforced stitching, water-resistant coatings, and fire-retardant properties to ensure reliability in harsh environments.
Outdoor & Recreational Gear
From camping gear to sporting equipment, custom textiles are vital in the outdoor industry. Weather-resistant fabrics are used for awnings, and protective coverings to shield against the elements.
Fire & Safety Equipment
Fire-resistant textiles are essential in industries where workers are exposed to high temperatures, spark and spall, or hazardous chemicals. A custom textile manufacturer can cut and sew custom products like welding curtains and industrial safety covers using materials that meet strict safety standards.
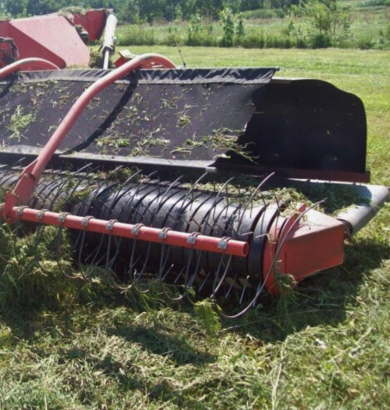
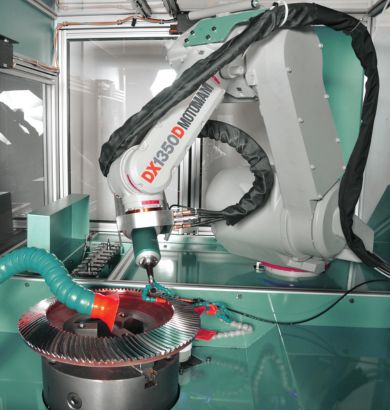
Industrial Equipment & Manufacturing
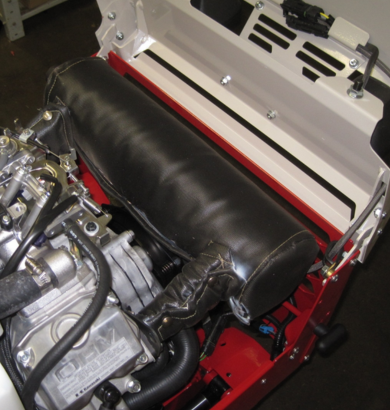
Powersports & Recreational Vehicles
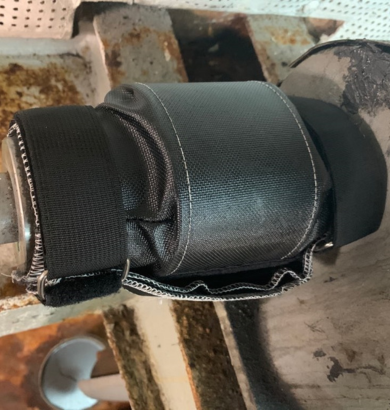
Military & Tactical Gear
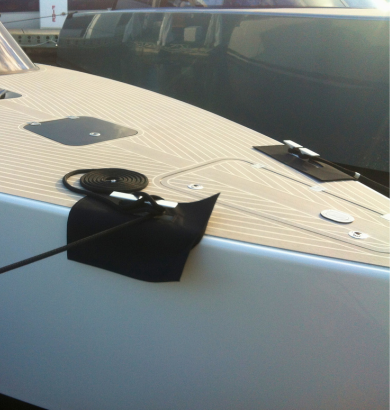
Outdoor & Recreational Gear
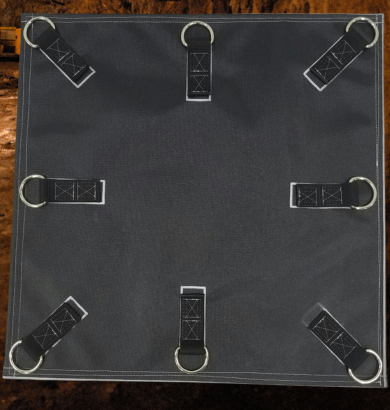
Fire & Safety Equipment
Selecting the Right Custom Textile Manufacturer
Choosing the right custom textile manufacturer is essential for ensuring a high-quality, cost-effective, and efficiently produced final product. Not all manufacturers offer the same level of expertise, capabilities, or service, so evaluating potential partners based on the following key factors will help you make an informed decision:
Reasonable Pricing
Cost varies depending on the complexity, materials, and production volume of your textile project. To find the right balance between price and quality, it’s advisable to request quotes from multiple manufacturers. While the lowest price may be tempting, a mid-range manufacturer with excellent reviews, customer support, and a proven track record often provides the best value.
Quality Materials & Superior Outcomes
The quality of materials directly impacts the durability, performance, and longevity of the final product. A reliable manufacturer should offer a range of high-quality textiles, ensuring your product exceeds functional expectations. Research potential manufacturers by reviewing past projects and requesting material samples to verify their standards. Seeing the materials firsthand and learning about their applications can provide valuable insights into the manufacturer’s capabilities.
Expert Design & Engineering Support
A skilled engineering team is crucial in guiding you through the design and production process. The right manufacturer will have expert design engineers who collaborate with you to refine your product concept, identify potential challenges, and optimize materials for performance. Using CAD modeling and prototyping, engineers can test designs early on, ensuring your final product functions as intended before mass production begins.
Prototyping & Testing Capabilities
Before committing to large-scale production, it's essential to test a prototype to validate functionality, durability, and performance. A manufacturer with in-house testing capabilities can help you refine your design, address any weaknesses, and confirm that the product meets industry standards. By working with a manufacturer that actively participates in testing, you reduce the risk of costly rework and ensure the final product performs as expected.
Quick Lead Times & Reliable Distribution
Timely production and distribution are essential for maintaining a reliable supply chain. A reputable manufacturer will be transparent about lead times, production schedules, and delivery commitments. Asking manufacturers about their typical turnaround times—and how they handle rush orders or unexpected delays - ensures you can plan accordingly and maintain consistent product availability.
Private Labeling Options
If you prefer to market products under your own brand name, private labeling may be an important consideration. Some manufacturers offer custom branding options, allowing your business name and logo to be featured on the final product without disclosing the original production source. This is particularly beneficial for companies that want to maintain brand exclusivity while outsourcing manufacturing.
Domestic vs Overseas Manufacturing
Choosing between domestic and overseas manufacturing affects production timelines, costs, and quality control. Domestic manufacturing offers several advantages, including faster lead times, easier communication, and the ability to tour facilities and meet teams in person. It also allows for greater oversight of quality assurance and compliance with industry regulations. While overseas options may provide cost savings, working with a domestic partner can streamline logistics and improve overall reliability.
Selecting the right custom textile manufacturer comes down to finding a partner that aligns with your quality expectations, budget, and production goals. By carefully considering pricing, materials, engineering expertise, lead times, and additional services like private labeling, you can establish a successful, long-term partnership that ensures your textile products meet and exceed expectations.
Maximizing Performance with Custom Textile Solutions
Custom textile manufacturing provides tailored solutions that enhance durability, protection, and efficiency across industries like agriculture, industrial equipment, and powersports. Choosing the right materials, manufacturing process, and production partner is essential to ensuring high-quality, cost-effective, and reliable textile products.
By working with a trusted manufacturer, you can benefit from expert engineering, rigorous testing, and efficient production, ensuring that textiles meet industry standards and performance expectations. Factors like quality materials, lead times, private labeling, and domestic production should be carefully considered when selecting a partner.
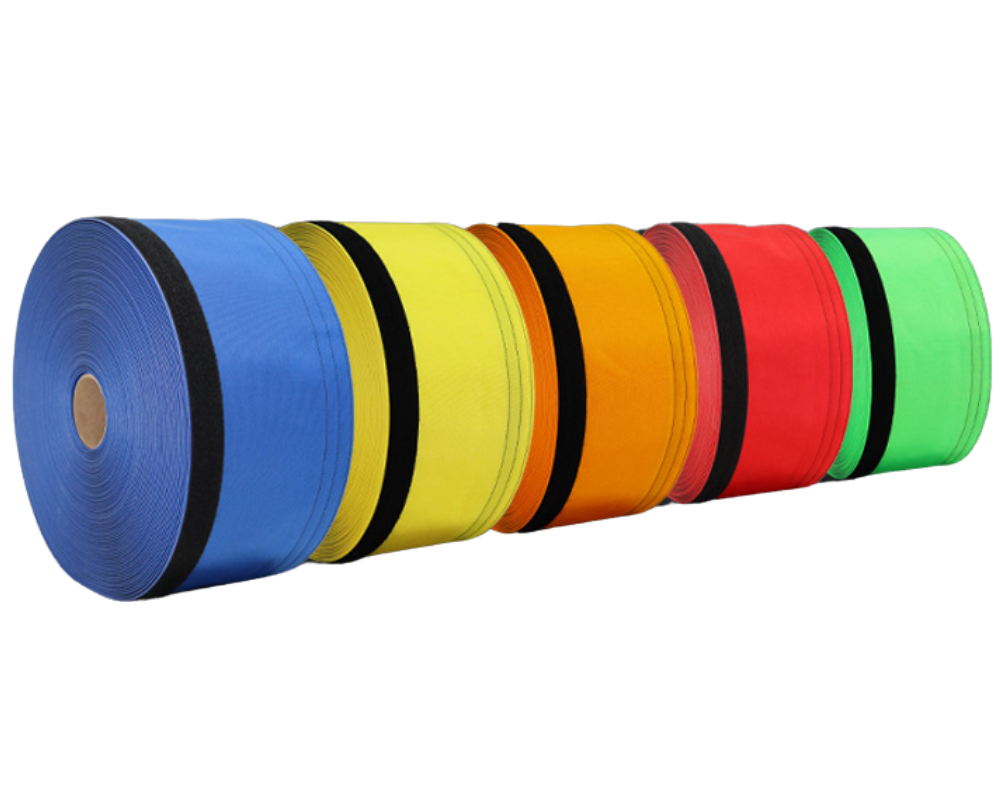
Maximizing Performance with Custom Textile Solutions
Custom textile manufacturing provides tailored solutions that enhance durability, protection, and efficiency across industries like agriculture, industrial equipment, and powersports. Choosing the right materials, manufacturing process, and production partner is essential to ensuring high-quality, cost-effective, and reliable textile products.
By working with a trusted manufacturer, you can benefit from expert engineering, rigorous testing, and efficient production, ensuring that textiles meet industry standards and performance expectations. Factors like quality materials, lead times, private labeling, and domestic production should be carefully considered when selecting a partner.