3 min read
Using ISO 8573-1 to Determine Air Treatment Solutions
Tsunami Team
:
Oct 18, 2022 9:00:00 AM
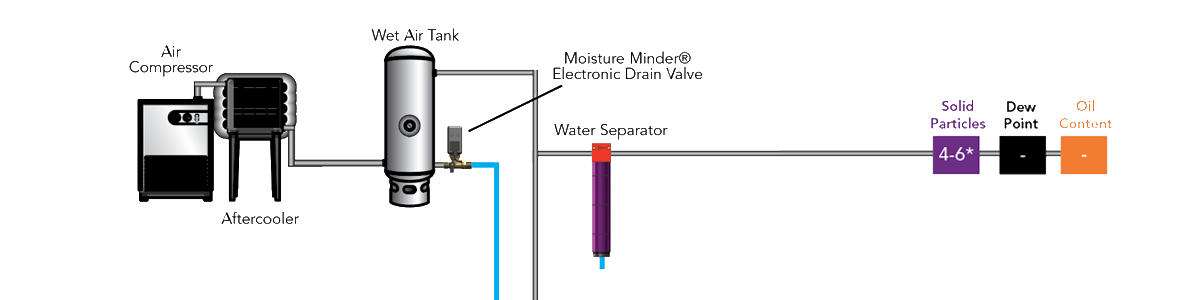
The delivery of compressed air to equipment in a workspace is more than removing condensation and maximizing the pressure available. ISO 8573-1 standards were established to outline impurity levels in compressed air and the air quality needed to supply equipment with adequate pressure.
Meeting ISO 8573-1 standards helps meet and comply with air quality requirements specified by equipment or application. Compliance with these standards is not mandatory. However, it may be set to a target range based on the industry where the compressed air is utilized.
Tsunami professionals collaborated to create a visual breakdown of the ISO 8573-1 classes and the specific components your compressed air system needs to meet those class standards and to achieve the best fit for your shop layout. The Tsunami Air Systems Schematic provides the right system setup to reach your desired ISO 8573-1 standard level and optimize production.
This blog will provide a deeper look into:
- ISO 8573-1 Explained
- Classification 0
- System Configuration and ISO 8573-1 Standard
- Using the Schematic
A Closer Look: ISO 8573-1 Standards Explained
The ISO 8573-1 Solid Particles Standards are divided into Classifications 1-6. In 2010, ISO 8573-1:2010 was added to help specify the purity of the compressed air required at a particular point in the system. Meanwhile, 8573-1 Parts 2 through 9 outline standards to test a compressed air system for one or more specific contaminants.
For the Oil Content Standards (separated into 9 classifications), Classification 1 specifies the amount of contamination allowable in each cubic meter of compressed air; 2:2018: Specifies the test method for oil aerosol content, and 3:1999: specifies the test method for the measurement of humidity.
Classification 4:2019: specifies the test method for particle content, 5:2001: specifies the test method for oil vapor and organic solvent content, and 6: 2003: specifies the test method for gaseous contaminant content.
Classification 7:2003: specifies the test method for viable microbiological contaminant content, 8:2004: specifies the test for solid particle content by mass concentration, and 9:2004: specifies the test method for liquid water content.
As for the other categories, there are Standard Classifications 1-6 for the Pressure Dew Point. For Class 1, the Pressure Dew Point is less than or equal to -100°F, while for Class 6, the Pressure Dew Point is less than or equal to 50°F.
Classification 0: Requirements and Misconceptions
Added in 2001, Class 0 shows stricter requirements can be necessary, based on specifications from unit operators or suppliers. However, this standard can be misapplied.
Contrary to popular belief, Class 0 does not mean zero contamination. It also does not mean or guarantee the compressed air is oil-free. It does not refer only to oil contamination, rather, Class 0 is cleaner than Class 1 for the contaminant specified. However, the contamination must be clearly stated. It requires the user or equipment operator to show the contamination level as part of the written specification. Class 0 is useless without a written specification, which should be included in all documentation.
Compressed Air System Configuration and ISO 8573-1 STANDARD
Tsunami Compressed Air Solutions provides customizable filter and dryer packages to fit your work area and the ISO 8573-1 standards that impact your final product.
The main components of an air system; air compressor, aftercooler, and wet air tank, are recommended as a standard best practice. The following additions allow the system to meet specific ISO 8573-1 specification and are outlined in the Tsunami Air Systems Schematic:
Adding the water separator to the base compressed air system allows your system to meet Class 4-6 ISO 8573-1 standards for solid particles.
The Tsunami Compressed Air Schematic also outlines the following configurations of the system:
Air Treatment Product | Solid Particles | Dew Point | Oil Content |
Water Separator | 4-6 | - | - |
Oil Coalescing Filter | 1-4 | - | 2-3 |
Activated Carbon Filter | - | - | 1-2 |
2-Stage Filter Package | 1-3 | - | 2-3 |
3-Stage Filter Package | 1-3 | - | 1-2 |
2-Stage Membrane Air Dryer | 1-3 | 3-5 | 2-3 |
3-Stage Membrane Air Dryer | 1-3 | 3-5 | 1-2 |
1 Regenerative Dryer | 1-3 | 1-3 | 2-3 |
2 Regenerative Dryers | 1-3 | 1-2 | 2-3 |
Regenerative Dryer with After Filter | 1-3 | 1-3 | 1-2 |
The consequences of an improperly configured system are two-fold.
A poorly configured system may allow the transfer of impurities to the finished product, thereby decreasing product quality.
If your compressed air system is not configured appropriately, it can also mean an increase in the maintenance budget, requiring parts replacement all too soon.
Clarify Setup Using the Tsunami Air System Schematic
ISO 8573-1 standards provide the most accurate testing guidelines to ensure air quality within a specific range. To optimize the setup of your compressed air system, follow the Tsunami Air System Schematic for a visual breakdown of the components needed to achieve the desired standards.
If your system may be falling short of a specific classification, the best way to resolve the issue is with the help of someone who knows the methods of success. Our Tsunami air system specialists can help you with any lingering questions about meeting ISO 8573-1 standards. Contact us today.
ISO 8573-1 | Keep Information Readily Available
Adjustments to your compressed air system may need to be made, based on the product lines in operation, workspace size, or equipment requiring optimal compressed air levels.
The Tsunami Air System Schematic is available for download and can be kept easily accessible for when these system changes are necessary. Fill out the form below for your printable download copy: