5 min read
5 Essential Tips for Hydraulic Hose Safety Covers
Python Covers Team
:
Jun 21, 2023 7:33:50 PM
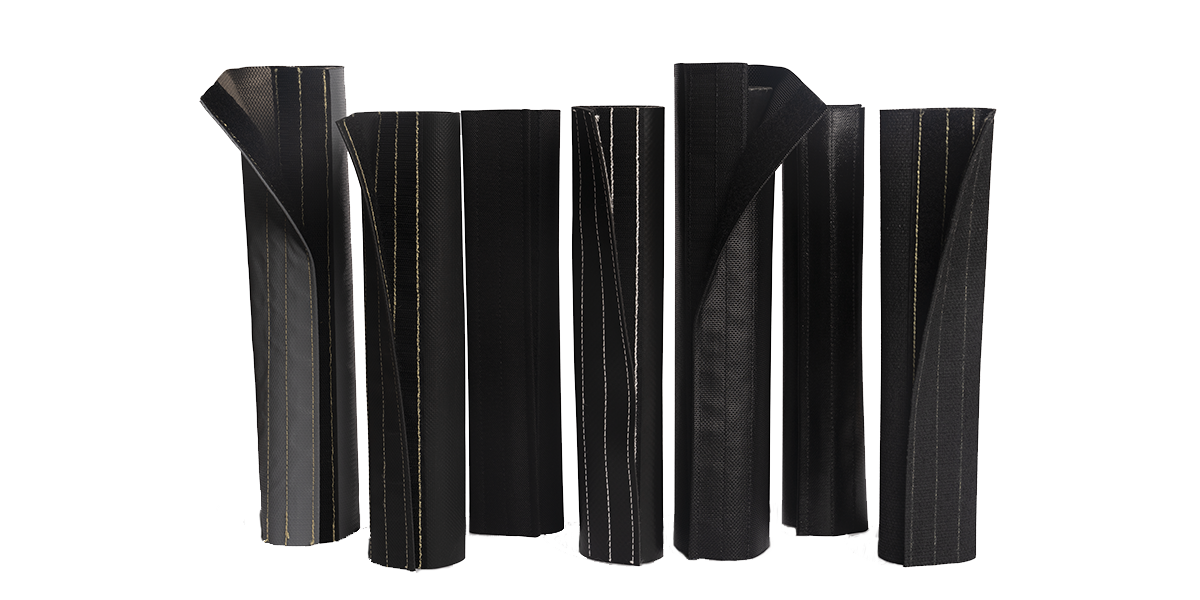
Hydraulic hoses are essential components of many machines, transferring pressurized liquids and gasses from one point to another. Without proper protection, these hoses can be unsafe - potentially causing leakages, fires, explosions, and other hazardous conditions.
There are a number of steps that can be taken to ensure safe use of hydraulic hoses. First and foremost (in our view) is having the right safety covers for an additional layer of protection against unfortunate accidents.
By following the practical guidelines below and using the right safety covers, you can make sure your hydraulic systems run efficiently with minimal risk to personnel and equipment on-site:
Hydraulic Hoses: 5 Steps for Hose Safety
Downtime on the job site is the last thing you want. An issue from a hydraulic hose, be it a leak or something more serious, is one of the fastest ways to outright stop work. Thinking ahead can protect the hydraulic hoses keeping your machinery in operation and your staff meeting deadlines.
These five steps for safer hydraulic hoses help keep things running like a well-oiled machine:
- Step 1: Select the Appropriate Safety Cover
- Step 2: Evaluate Hydraulic Hose Systems
- Step 3: Proper Installation of Safety Covers
- Step 4: Regular Inspection and Regular Maintenance
- Step 5: Train and Educate Employees
Step 1: Select the Appropriate Safety Cover
Safety covers for hydraulic hoses provide an extra layer of protection from potential hazards. They offer a physical barrier that helps to both protect personnel and equipment on-site. A safety cover also minimizes the risk of damage to the hose or its surrounding environment.
With a safety cover in place, any trouble with the hose can be spotted quickly and dealt with without endangering anyone or anything nearby. They can also reduce noise levels and lessen the chance of fire, promoting a safer working environment overall.
Three major factors – all of which put considerable wear and tear on a hose – to consider when selecting safety covers for hydraulic hoses include:
- Temperature
- Pressure
- Environment
It’s important to understand the different types of safety covers available for hydraulic hoses in order to properly secure them and prevent leakages. Commonly used safety covers are nylon and other textile options, wire braid, canvas, or stainless steel wrap.
-
Nylon: Provides superior abrasion resistance compared to other types of safety covers making them well-suited for use in environments where hoses may come into contact with sharp edges or abrasive components. Due to their high flexibility, they can be used in tight spaces that don't allow for the installation of a traditional wire braid or canvas covers. In extreme cases, nylon covers are often used to provide additional insulation from extreme temperature fluctuations and higher pressures.
-
Wire Braid: Used for higher-pressure hoses, because it provides additional protection from external elements and helps reduce wear due to friction.
-
Canvas: Acts as a cushioning layer for hoses exposed to harsh environments such as pipes with sharp edges or abrasion on the equipment.
-
Stainless Steel: Provides excellent corrosion resistance and can be ideal when working with extreme temperatures and high-pressure applications.
Step 2: Evaluate Hydraulic Hose Systems
The next step in ensuring the safest use of hydraulic hoses in your facility is to assess the hydraulic hose systems and identify potential risks and vulnerabilities. Among the most common issues include:
- Kinks: The flow of fluid can be obstructed, leading to potential breakdowns and even dangerous explosions.
- Bulges: This indicates a weak spot in the hose system, which can lead to failure.
- Wear and tear: This indicates a potential spot where leaks or other issues can occur.
- Obstructions: Blockages preventing fluid from flowing.
- Leaks: Any leak is a concern, as it can lead to bigger problems; pinhole leaks can cause worker injury or even death.
Be certain you are familiar with the type of equipment used and its associated risk levels before installing new systems or components. Confirm all connections are secure and snug to prevent incidents involving leakages. Hose clamps and banding should be checked regularly to ensure they are properly tightened.
During maintenance, hose cover inspection is essential; look for abrasions, tears, snags, or cuts in the protective material. These can weaken the strength of the hose and make it vulnerable to further damage. This should also be a top priority any time new components are installed.
Abrasions, in particular, can cause deeper damage as they can create a pathway for liquids or gasses to escape from the hose – which could result in a dangerous situation. Be sure to check those areas regularly for wear and tear as it can affect the performance of the system.
It's also essential to understand how hydraulic systems work and where the specific components are located in order to be able to identify potential risks properly.
Step 3: Proper Installation of Safety Covers
When installing safety covers, the cover should be securely fastened to the hose, using the appropriate clamps or bands. It’s important the clamps are easy to open and close but tight enough so they do not loosen over time. When sealing the ends of the hose with safety covers, ensure any gaps between the safety cover and hose ends are sealed properly to prevent leaks or escapes from occurring.
For a secure and snug fit for the hydraulic hose, the clamps should be checked regularly and tightened if necessary. The best way to do this is to use adjustable locking pliers or wrenches to get the right amount of clamping force. When using safety covers, check the edges of the cover for any signs of tearing or fraying as it could lead to leakage.
Step 4: Regular Inspection and Maintenance
Regularly inspect and maintain hydraulic hose covers to ensure the safety of personnel and equipment operating around them. A good rule of thumb is to carry out maintenance checks every six months, or more often if the hose covers are exposed to extreme conditions or frequent movement. This should include a thorough visual inspection of the cover and any connections, clamps, seals, and other components.
For comprehensive maintenance, follow this checklist:
- Check for signs of wear and tear such as tears, rips, fraying fabric, or discoloration
- Inspect all connections for proper tightness and sealing
- Visually identify any areas that may be susceptible to abrasion or corrosion
- Check for any signs of leaks or fluid seepage
- Make sure all components are securely fastened to avoid shifting or loosening
Step 5: Train and Educate Employees
Educating your employees on the safety and proper use of hydraulic hoses is a key part of maintaining the integrity of the system. The only thing more dangerous than a compromised hydraulic hose about to fail is an employee who can’t identify the warning signs to begin with. Employee training should focus on:
- How to inspect a hose for signs of wear and tear
- The importance of regularly checking connections and seals
- How to identify areas that may be susceptible to abrasion or corrosion
- The dangers associated with leaking or seeping fluids
- How to properly fasten components and avoid shifting or loosening
It’s important for employees to be familiar with the types of protective equipment they should use when handling a hydraulic hose. PPE clothing such as gloves, goggles, and steel-toe boots can help prevent serious injury if any fluid should spray or leak out.
By training your staff on all aspects of OSHA hydraulic hose safety, you can ensure that your workplace remains safe and in compliance with regulations.
Additional training considerations:
- Visual aids for employees learning hydraulic hose safety regulations.
- Demonstrations of how to properly inspect a hose and how to fit components together securely to illustrate why safety is so important.
- Practice drills to help employees become familiar with the proper procedure and remember key steps in the process.
- Assigning a mentor or experienced employee to show new workers the ropes to ensure everyone knows the safety protocols.
- Provide adequate information for your staff. Provide safety manuals or detailed instructions that outline proper techniques and procedures. These documents should include topics such as materials selection, proper assembly methods, potential hazards associated with hydraulic hoses, and what to do in an emergency if a fluid leak occurs or a system fails.
Hydraulic Hose Safety Covers: Planning Ahead
Hydraulic hose safety covers are an important component of safety protocols for workers, as they limit the risk of injury or death due to contact with high-pressure fluids. They should be inspected regularly to ensure their integrity and replaced when necessary. Having a designated team member or supervisor who knows how to properly install and replace these covers is also beneficial.
It’s important to have a plan to address any potential problems, such as if a hose becomes damaged or fails unexpectedly and provide your staff with detailed information on what actions should be taken in the event of such an occurrence. As an employer, you should ensure all employees understand the importance of hydraulic hose safety covers and why they must be used when working with pressurized systems.