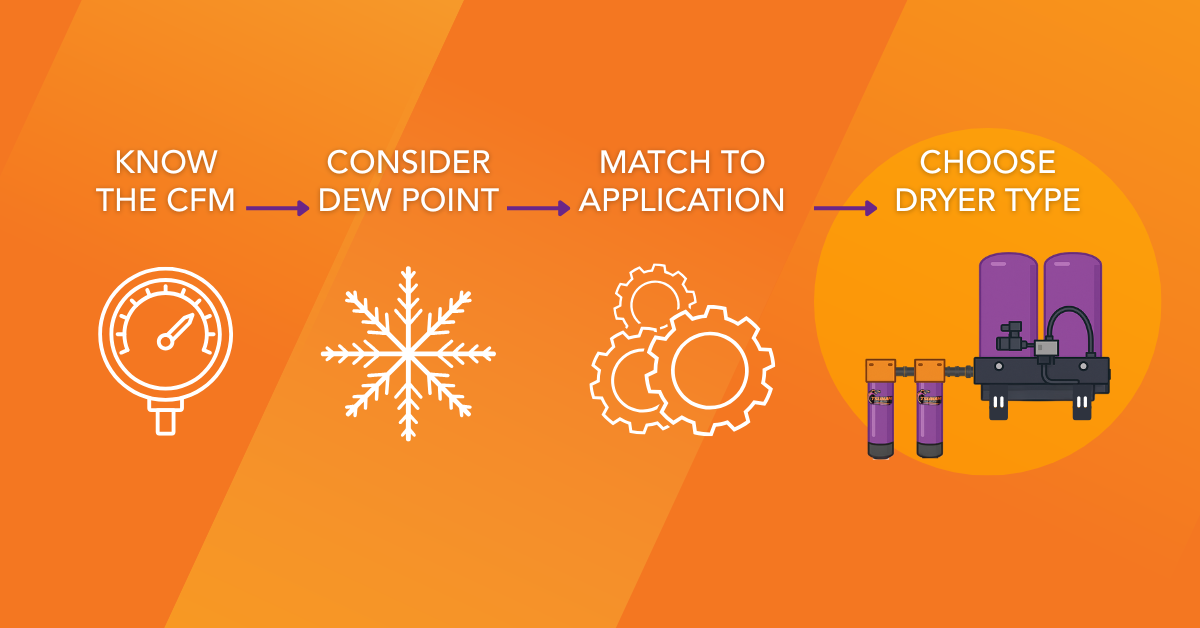
Dryers are critical to reducing the moisture in the compressed air that powers your tools and machinery. Without them, both the quality and performance of your machines can regress, slowing down your business’s productivity.
While the decision to use a compressed air dryer may be an easy one, the choice in size may not be as simple. Why? Because there are so many styles to choose from – and so many repercussions for selecting the wrong size. While your manufacturer can guide you through the selection process, understanding the factors that affect dryer size can make the process quicker and easier.
Below, we’ll talk about the factors that affect compressed air dryer sizing to set you up for success.
- Why does sizing matter for compressed air dryers?
- Factors affecting compressed air dryer sizing
- How to tell if your dryer is the wrong size
- Bonus tips for choosing the right compressed air dryer size
- Choosing the right Tsunami compressed air dryer
Why does sizing matter for compressed air dryers?
Choosing the right sized compressed air dryer ensures efficiency, reliability, and optimized cost.
If you choose an air dryer that’s too small for your machine, it’ll be unable to completely remove moisture from the compressed air system, compromising your machine’s performance and quality. In other words, moisture buildup can lead to rust – or worse – complete machine failure. In food industry applications, health and safety can be at risk.
Choose an air dryer that’s too big on the other hand, and you’ll waste energy and money.
To put it simply, choosing the correct compressed air dryer sizing extends the longevity of your machines, and avoids overspending on dryers expending excessive energy.
Factors affecting compressed air dryer sizing
Before you can decide on the right size of air dryer, it’s critical to understand which factors will affect your choice. Keep in mind, these factors will fluctuate. Because of these fluctuations, most manufacturers provide correction measures to account for changes in temperature, pressure, or other conditions.
Let’s take a look at the key determining factors and discover how to find this crucial information:
- Flow Rates (CFM)
- Pressure Dew Point (PDP)
- Air Pressure (PSI)
- Inlet Air Temperature
- Ambient Air Temperature
- Air Quality Standards
Flow Rates (CFM)
Flow rate, measured in CFM (cubic feet per minute), refers to how much air an air compressor can deliver over time. This will vary based on the air compressor you’re using, and typical flow rates range from 5-120 CFM. For example, membrane dryers typically operate at 15-20 CFM, while some desiccant dryers can reach up to 400 CFM.
In general, your air dryer should have a 10-20% higher CFM than your compressor’s maximum CFM. That’s to account for any fluctuations in moisture, temperature, etc. Your compressor’s manufacturer can help you identify the maximum CFM of your air system.
Pressure Dew Point (PDP)
Pressure dew point, or PDP, measures the moisture content in compressed air. In other words, it’s the temperature at which vapor turns to liquid water at a specific pressure. Knowing this temperature will help you avoid excessive moisture buildup in your air system and help you choose the appropriate dryer for your application.
The lower the PDP, the drier the air. For desiccant and membrane air dryers, PDP is typically from 0 down to -40°F, while refrigerated air dryers have a PDP from 37°F – 50°F. If you’re unsure of the PDP of your system, contact the manufacturer.
Air Pressure (PSI)
The amount of pressure (PSI) your air system holds impacts the amount of moisture it will hold, directly affecting the amount of drying required. You can typically find the maximum operating PSI of your compressor on the product brochure or by reaching out to the manufacturer.
Inlet Air Temperature
Inlet air temperature is the temperature of the air entering the dryer. Standard inlet temperatures for compressed air dryers is 100°F. The higher the inlet temperature, the higher the moisture, requiring more drying capacity. If the temperature gets too high, your air quality will be compromised.
Ambient Air Temperature
On the other hand, ambient air temperature measures the external temperature surrounding your air system. The warmer the temperature of your facility, the harder your dryer will have to work to reduce moisture. The cooler the facility, the more productive the dryer will be.
Ambient temperature can vary for mobile operations like spray foam because the systems are working on mobile rigs. Shifting ambient temperatures due to mobility – especially in extreme heat or cold – can impact dryer moisture levels and performance.
Air Quality Standards
Air quality standards will determine the amount of drying capacity you’ll need. The more stringent air quality your application requires, the more drying capacity you’ll need, likely requiring a larger dryer or alternative dryer technology. Air quality standards vary by industry, but ISO 8573-1 is universally used to ensure adequate air quality.
Check out this article on ISO 8573-1, where our team breaks down air quality standards for different compressor types, applications, and industries.
How to tell if your dryer is the wrong size
If you’re curious whether your current air dryer is the wrong size, here are some indications that you may need to size up:
- Moisture buildup
- Rusting
- Contamination in moisture or oil buildup
- Poor quality in materials produced using the compressed air system
- Frequent system failures
Alternatively, here are some signs your dryer is too big, and a smaller size is a better fit:
- Frequent cycling on and off
- Higher energy costs
- Higher operational costs than the up-front cost of the dryer
Bonus tips for choosing the right compressed air dryer size
When sizing your compressed air dryer, keep these tips in mind:
- Use correction factors: Compressors are typically rated using the standard conditions for air dryers - that is 100°F for inlet and ambient air temperature, 100 PSI, and 100% air saturation. Corrective factors are measures you can implement based on the system's actual operating conditions. These measures help optimize your drying capacity.
- Consider an aftercooler: This is an additional measure you can take to maximize you compressed air system's output. It works by reducing the moisture content in the incoming air before it reaches the compressor. This can be especially useful in high-moisture, warm, or mobile environments like spray foam applications.
- Take advantage of filters: Filters can work together with dryers to maximize system performance and in most applications should be considered a requirement. They can also prevent water from entering the compressor system, presenting an additional obstacle for excess moisture. Talk to your manufacturer about whether you need a compressed air filter.
- Check your documentation: Typically, manufacturers will provide you with the product's specifications in the form of a data sheet or brochure/manual. If you don't have it already, contact the manufacture or visit their website.
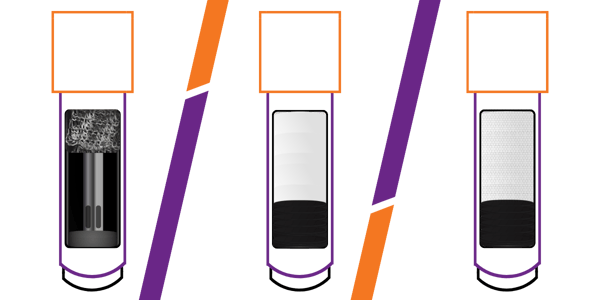
Choosing the right Tsunami compressed air dryer
Whether you’re looking for a refrigerated, membrane, or desiccant air dryer, Tsunami provides you with all the product specs and additional moisture-fighting measures you’ll need for a long-lasting, efficient air system.
Curious about whether you have the right compressor size for your facility? The experts at Tsunami are here to help. Contact us today to discuss the specifics of your compressed air system and see how we can help you find a cost-effective fit.